A wireless sensor-based cable force and bending stiffness monitoring method and system
A wireless sensor, bending stiffness technology, applied in the testing of machine/structural components, testing of mechanical components, instruments, etc., can solve the problem of reducing the accuracy of data calculation and processing, increasing the power consumption of data transmission, and the inability to calculate the bending resistance of cable structures Stiffness and other issues
- Summary
- Abstract
- Description
- Claims
- Application Information
AI Technical Summary
Problems solved by technology
Method used
Image
Examples
Embodiment Construction
[0067] The following will clearly and completely describe the technical solutions in the embodiments of the present invention with reference to the accompanying drawings in the embodiments of the present invention. Obviously, the described embodiments are only some, not all, embodiments of the present invention. Based on the embodiments of the present invention, all other embodiments obtained by persons of ordinary skill in the art without creative efforts fall within the protection scope of the present invention.
[0068] refer to figure 1 , is a schematic flowchart of a wireless sensor-based cable force and bending stiffness monitoring method provided by an embodiment of the present invention.
[0069] Step (1), use the wireless sensor to obtain the cable vibration acceleration signal corresponding to the cable structure, and perform Welch transformation processing on the cable vibration acceleration signal to obtain the corresponding cable vibration acceleration signal powe...
PUM
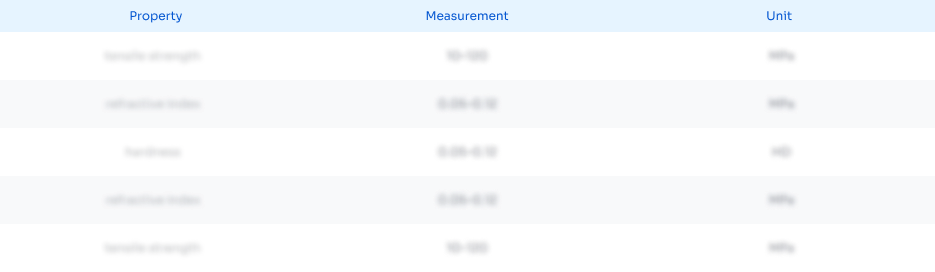
Abstract
Description
Claims
Application Information

- R&D Engineer
- R&D Manager
- IP Professional
- Industry Leading Data Capabilities
- Powerful AI technology
- Patent DNA Extraction
Browse by: Latest US Patents, China's latest patents, Technical Efficacy Thesaurus, Application Domain, Technology Topic, Popular Technical Reports.
© 2024 PatSnap. All rights reserved.Legal|Privacy policy|Modern Slavery Act Transparency Statement|Sitemap|About US| Contact US: help@patsnap.com