Smelting furnace
A smelting furnace and furnace body technology, applied in the field of smelting furnaces, can solve the problems of low smelting efficiency and high energy consumption, and achieve the effects of good smelting effect, low energy consumption and uniform stress
- Summary
- Abstract
- Description
- Claims
- Application Information
AI Technical Summary
Problems solved by technology
Method used
Image
Examples
Embodiment Construction
[0029] The present invention will be described in further detail below in conjunction with the accompanying drawings and embodiments. It should be understood that the specific embodiments described here are only used to explain the present invention, not to limit the present invention.
[0030] Please see figure 1 , is a structural schematic diagram of a preferred embodiment of a smelting furnace according to the present invention. A smelting furnace includes: a furnace body 1 , a furnace roof 2 , an exhaust flue 3 , and a plurality of spray guns 4 .
[0031] Inside the furnace body 1 is a cavity 11 with an open upper end. The cavity 11 has a small diameter area 111 and a large diameter area 112 above the small diameter area 111. The small diameter area 111 and the large diameter area 112 have a circular cross section. , the inner diameter of the large diameter area 112 is larger than the inner diameter of the small diameter area 111 . Electronic waste, copper-containing mat...
PUM
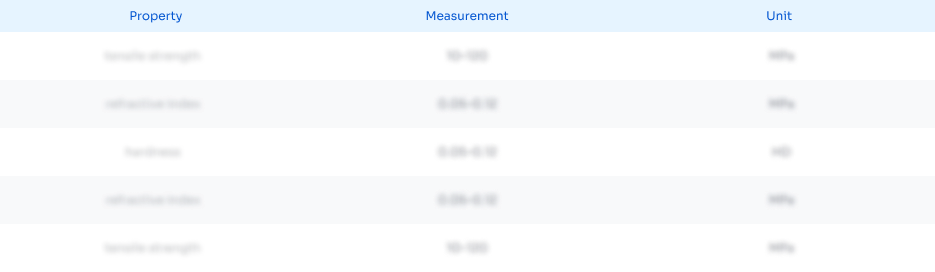
Abstract
Description
Claims
Application Information

- Generate Ideas
- Intellectual Property
- Life Sciences
- Materials
- Tech Scout
- Unparalleled Data Quality
- Higher Quality Content
- 60% Fewer Hallucinations
Browse by: Latest US Patents, China's latest patents, Technical Efficacy Thesaurus, Application Domain, Technology Topic, Popular Technical Reports.
© 2025 PatSnap. All rights reserved.Legal|Privacy policy|Modern Slavery Act Transparency Statement|Sitemap|About US| Contact US: help@patsnap.com