A Scissor Bending Metamorphic Mechanism Manipulator
A metamorphic mechanism and manipulator technology, applied in manipulators, aerospace equipment, chucks, etc., can solve the problems of small grasping scale, single design mode, and high quality of articulated manipulators
- Summary
- Abstract
- Description
- Claims
- Application Information
AI Technical Summary
Problems solved by technology
Method used
Image
Examples
Embodiment Construction
[0038] The technical solutions in the embodiments of the present application will be clearly and completely described below in conjunction with the accompanying drawings in the embodiments of the present application. Obviously, the described embodiments are only examples and not intended to limit the present application.
[0039] A scissors bending metamorphic mechanism manipulator provided by the embodiment of the present invention, such as figure 1 As shown, it includes: an installation platform 1, a plurality of manipulator claws 2 installed on the installation platform 1, and a drive unit 3 connected to each manipulator claw 2 for driving the movement of the corresponding manipulator claw 2; wherein,
[0040] Such as figure 2 As shown, each manipulator 2 includes a plurality of metamorphic mechanism units 4 connected end to end along the folding direction (that is, connected in series), figure 2 Take the manipulator 2 as an example to include two metamorphic mechanism u...
PUM
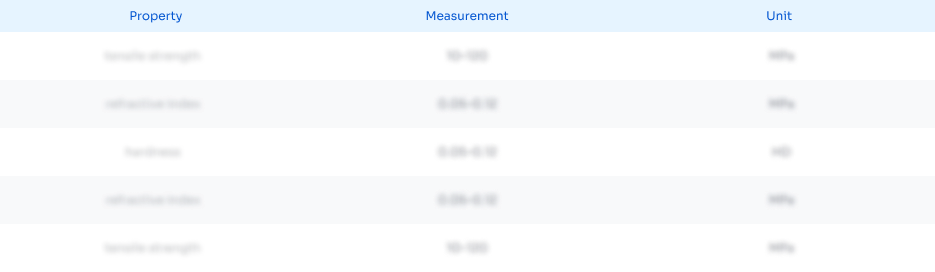
Abstract
Description
Claims
Application Information

- Generate Ideas
- Intellectual Property
- Life Sciences
- Materials
- Tech Scout
- Unparalleled Data Quality
- Higher Quality Content
- 60% Fewer Hallucinations
Browse by: Latest US Patents, China's latest patents, Technical Efficacy Thesaurus, Application Domain, Technology Topic, Popular Technical Reports.
© 2025 PatSnap. All rights reserved.Legal|Privacy policy|Modern Slavery Act Transparency Statement|Sitemap|About US| Contact US: help@patsnap.com