A kind of preparation method of surface-modified graphene waterborne polyurethane anticorrosion coating
A technology for anti-corrosion coatings and surface modification, applied in polyurea/polyurethane coatings, anti-corrosion coatings, coatings, etc., can solve the problems of poor anti-corrosion effect, achieve the effects of not being easy to pulverize, reduce coating thickness, and improve wear resistance Effect
- Summary
- Abstract
- Description
- Claims
- Application Information
AI Technical Summary
Problems solved by technology
Method used
Image
Examples
Embodiment 1
[0021] A preparation method for surface-modified graphene water-based polyurethane anticorrosion coating, comprising the following steps:
[0022] 1) Preparation of graphite oxide powder: immerse 10g of ground graphite powder in 200ml of concentrated nitric acid, soak for 1h at 0°C, cool down to -15°C, add 1ml of concentrated phosphoric acid and 40g of potassium ferrate, react at 60°C for 0.5h and then centrifuge , washing the filter cake with deionized water until the pH of the washing solution is 6-7, placing it in a vacuum drying oven, and drying at 70°C for 4 hours to obtain graphite oxide powder;
[0023] 2) Preparation of multilayer graphite powder: graphite oxide powder containing NaBH 4 and CaCl 2 After soaking in the solution for 10 hours, filter, wash the filter cake with deionized water, and then dry it in a drying oven at 60°C for 6 hours to obtain multilayer graphite powder;
[0024] 3) Preparation of modified graphene powder: soak the multilayer graphite powder...
Embodiment 2
[0029] A preparation method for surface-modified graphene water-based polyurethane anticorrosion coating, comprising the following steps:
[0030] 1) Preparation of graphite oxide powder: immerse 10g of ground graphite powder in 200ml of concentrated nitric acid, soak at 0°C for 1.5h, cool down to -15°C, add 1ml of concentrated phosphoric acid and 40g of potassium ferrate, react at 25°C for 14h and then centrifuge , washing the filter cake with deionized water until the pH of the washing solution is 6-7, placing it in a vacuum drying oven, and drying at 65°C for 5 hours to obtain graphite oxide powder;
[0031] 2) Preparation of multilayer graphite powder: graphite oxide powder containing NaBH 4 and CaCl 2 Soak in the solution for 9 hours and then filter, wash the filter cake with deionized water and dry it in a drying oven at 60°C for 6 hours to obtain multi-layered graphite powder;
[0032] 3) Preparation of modified graphene powder: soak the multilayer graphite powder obt...
Embodiment 3
[0037] A preparation method for surface-modified graphene water-based polyurethane anticorrosion coating, comprising the following steps:
[0038]1) Preparation of graphite oxide powder: immerse 10g of ground graphite powder in 200ml of concentrated nitric acid, soak at 0°C for 2h, cool down to -15°C, add 1ml of concentrated phosphoric acid and 40g of potassium ferrate, react at -10°C for 24h and then centrifuge , washing the filter cake with deionized water until the pH of the washing solution is 6-7, placing it in a vacuum drying oven, and drying at 60°C for 6 hours to obtain graphite oxide powder;
[0039] 2) Preparation of multilayer graphite powder: graphite oxide powder containing NaBH 4 and CaCl 2 Soak in the solution for 8 hours and then filter, wash the filter cake with deionized water and dry it in a drying oven at 60°C for 6 hours to obtain multi-layered graphite powder;
[0040] 3) Preparation of modified graphene powder: soak the multilayer graphite powder obtai...
PUM
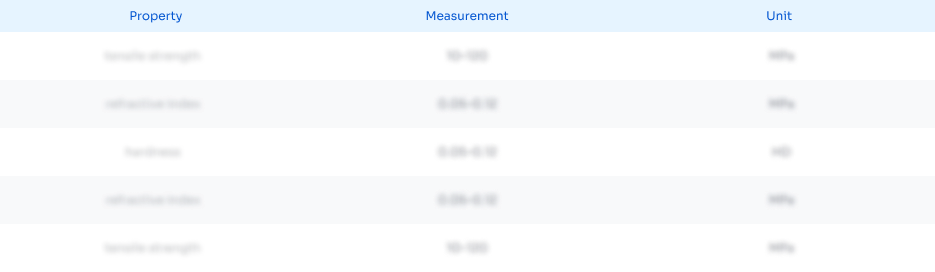
Abstract
Description
Claims
Application Information

- R&D Engineer
- R&D Manager
- IP Professional
- Industry Leading Data Capabilities
- Powerful AI technology
- Patent DNA Extraction
Browse by: Latest US Patents, China's latest patents, Technical Efficacy Thesaurus, Application Domain, Technology Topic, Popular Technical Reports.
© 2024 PatSnap. All rights reserved.Legal|Privacy policy|Modern Slavery Act Transparency Statement|Sitemap|About US| Contact US: help@patsnap.com