Micro-texture radial vibration auxiliary electrolytic machining method and device for inner wall of rotary body of thin-wall part
A technology of radial vibration and processing method, which is applied in the direction of electric processing equipment, electrochemical processing equipment, accessory devices, etc., can solve the problems of low processing performance and difficult discharge of processed products, so as to improve processing accuracy, reduce stray corrosion, The effect of short preparation cycle
- Summary
- Abstract
- Description
- Claims
- Application Information
AI Technical Summary
Problems solved by technology
Method used
Image
Examples
Embodiment Construction
[0021] The present invention will be further described below in conjunction with the accompanying drawings.
[0022] refer to Figure 1 to Figure 4 , a radial vibration-assisted electrolytic machining method for micro-textured internal walls of a thin-walled part, wherein the cathode of a tool capable of radial vibration with a micro-convex texture on the surface is connected to the negative pole of a power supply, and the cathode of the tool is connected to an ultrasonic current generator The thin-walled rotary workpiece is connected to the positive pole of the power supply, and the columnar electrodes on the tool cathode are arranged in a linear array; the electrolyte enters the reaction area between the tool cathode and the workpiece through the liquid supply pipe, and participates in the electrochemical reaction between the tool cathode and the workpiece. Response: The machine tool spindle drives the tool cathode to move along the circumferential direction according to the...
PUM
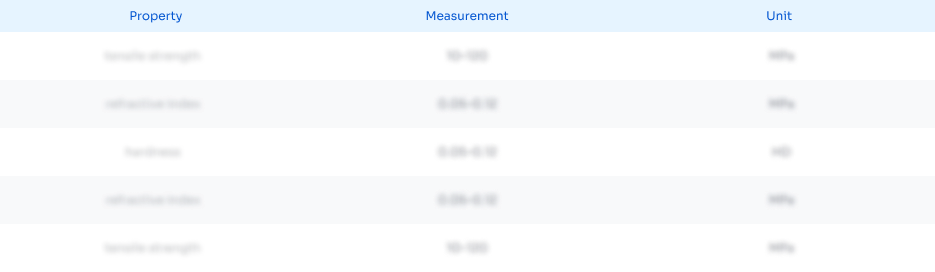
Abstract
Description
Claims
Application Information

- Generate Ideas
- Intellectual Property
- Life Sciences
- Materials
- Tech Scout
- Unparalleled Data Quality
- Higher Quality Content
- 60% Fewer Hallucinations
Browse by: Latest US Patents, China's latest patents, Technical Efficacy Thesaurus, Application Domain, Technology Topic, Popular Technical Reports.
© 2025 PatSnap. All rights reserved.Legal|Privacy policy|Modern Slavery Act Transparency Statement|Sitemap|About US| Contact US: help@patsnap.com