Quasi-zero stiffness vibration isolation system
A vibration isolation system and quasi-zero stiffness technology, applied in the direction of shock absorbers, spring/shock absorber functional characteristics, springs, etc., can solve problems such as difficulty in maintaining equipment stability, inability to effectively compete, and low stiffness, etc., to achieve Solve instability, good vibration isolation effect, and reduce the effect of vertical stiffness
- Summary
- Abstract
- Description
- Claims
- Application Information
AI Technical Summary
Problems solved by technology
Method used
Image
Examples
Embodiment Construction
[0020] In order to further illustrate the technical means and effects adopted by the present invention to solve the technical problems, the present invention will be described in further detail below with reference to the accompanying drawings and specific embodiments. It should be noted that the provided drawings are schematic, and are not mutually The drawings and specific embodiments are not completely drawn to size or scale, and therefore the drawings and specific embodiments are not intended to limit the scope of protection claimed by the present invention.
[0021] like figure 1 The shown alternative embodiment of the quasi-zero stiffness vibration isolation system includes a negative stiffness module 2 and a plurality of positive stiffness modules 1 connected in parallel with it, the negative stiffness modules 2 are arranged in a geometrical arrangement formed by the plurality of positive stiffness modules 1. The center position of the graph. In this embodiment, a neg...
PUM
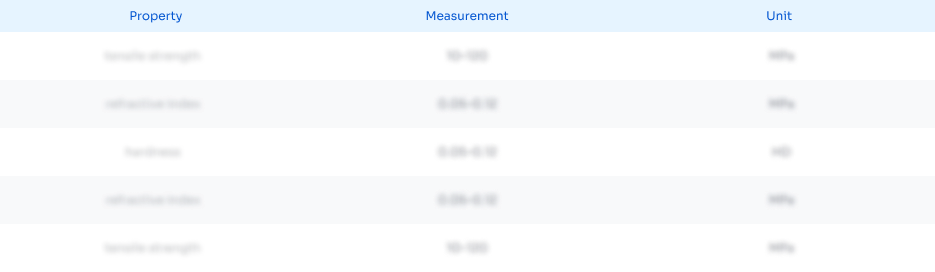
Abstract
Description
Claims
Application Information

- R&D
- Intellectual Property
- Life Sciences
- Materials
- Tech Scout
- Unparalleled Data Quality
- Higher Quality Content
- 60% Fewer Hallucinations
Browse by: Latest US Patents, China's latest patents, Technical Efficacy Thesaurus, Application Domain, Technology Topic, Popular Technical Reports.
© 2025 PatSnap. All rights reserved.Legal|Privacy policy|Modern Slavery Act Transparency Statement|Sitemap|About US| Contact US: help@patsnap.com