Shoulder joint working method based on bionic structure
A working method and shoulder joint technology, applied in the field of bionic machinery, can solve the problems of insufficient lightness in structure, large volume and difficult operation, and achieve the effects of simple and novel structure, simple operation and convenient operation.
- Summary
- Abstract
- Description
- Claims
- Application Information
AI Technical Summary
Problems solved by technology
Method used
Image
Examples
Embodiment 1
[0035] A shoulder joint working method based on a bionic structure, based on a bionic shoulder joint mechanism, the bionic shoulder joint mechanism includes a flexion and extension device and an extension and extension device; the flexion and extension device includes two symmetrically arranged T-shaped plates 2, two T-shaped plates 2 An end plate is arranged between, and an upper gear set is arranged on the end plate, and the upper gear set includes two gears meshing in sequence, and a first motor 16 is arranged on the end plate, and the first motor 16 is connected with the gear at the top of the upper gear set; The stretching device includes a U-shaped connecting plate 8, and the U-shaped connecting plate 8 is provided with a connecting block 24, a second motor 9 and a lower gear set. The lower gear set includes two meshing gears, and the connecting block includes four sides, two of which One opposite side is connected with the terminal gear of upper gear set by rotating shaf...
Embodiment 2
[0040]A shoulder joint working method based on a bionic structure, the steps of which are as described in Embodiment 1, the difference is that the upper gear set of the bionic shoulder joint mechanism includes three sequentially meshed gears, and the gear at the top of the upper gear set rotates , driving the three gears meshing in turn to rotate. Three gears are provided to increase the motion angle of the ball joint mechanism, which can prevent motion interference during the flexion and extension of the ball joint. Setting too many gears will reduce the transmission efficiency and increase the mass and volume of the mechanism.
Embodiment 3
[0042] A shoulder joint working method based on a bionic structure, its steps are as described in Embodiment 2, the difference is that the number of upper gear sets on the end plate of the bionic shoulder joint mechanism is two rows, and one row of upper gear sets is vertical The first gear 14, the third gear 13, and the fifth gear 12 are arranged in the direction, and the second gear 19, the fourth gear 21, and the sixth gear 22 are vertically arranged on the other row of upper gear sets; the first motor includes the first output of the first motor Shaft 15 and the second output shaft 18 of the first motor, the first output shaft 15 of the first motor is connected with the first gear 14, and the second output shaft 18 of the first motor is connected with the second gear 19, as figure 2 shown.
[0043] When the first motor is driven, the two output shafts of the first motor rotate simultaneously, driving the first gear and the second gear to rotate, the first gear drives the ...
PUM
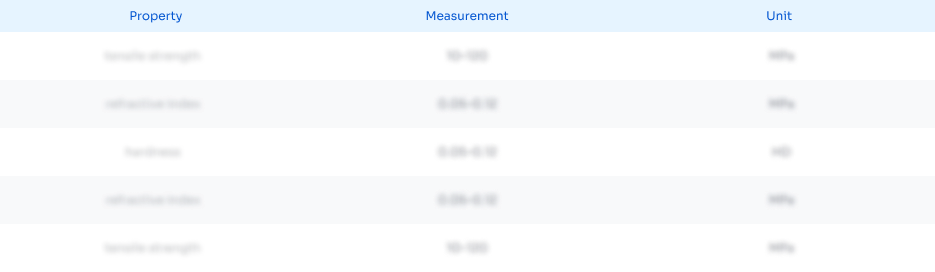
Abstract
Description
Claims
Application Information

- R&D
- Intellectual Property
- Life Sciences
- Materials
- Tech Scout
- Unparalleled Data Quality
- Higher Quality Content
- 60% Fewer Hallucinations
Browse by: Latest US Patents, China's latest patents, Technical Efficacy Thesaurus, Application Domain, Technology Topic, Popular Technical Reports.
© 2025 PatSnap. All rights reserved.Legal|Privacy policy|Modern Slavery Act Transparency Statement|Sitemap|About US| Contact US: help@patsnap.com