An Adaptive Robust Sliding Mode Control Method for a Hybrid Robot for Automobile Electrophoretic Coating Conveying
An adaptive robust, electrophoretic coating technology, applied in the direction of adaptive control, general control system, control/regulation system, etc. Guarantee problems such as sliding mode, avoid saturation and chattering phenomenon, and suppress chattering
- Summary
- Abstract
- Description
- Claims
- Application Information
AI Technical Summary
Problems solved by technology
Method used
Image
Examples
Embodiment 1
[0118] The present invention mainly focuses on using an adaptive robust sliding mode control method to improve the motion control performance of the hybrid robot for automobile electrophoretic coating transportation. This method can not only enhance the robustness and anti-interference ability of the system, but also can Suppresses chattering in sliding mode control and resolves actuator saturation. The block diagram of the adaptive robust sliding mode control principle of the new hybrid robot for electrophoretic coating transportation is as follows: figure 2 As shown, the specific implementation of the control method is as follows:
[0119] 1. Solve the Jacobian matrix
[0120] exist figure 1 In this method, the rod length constraint equation is used, and the kinematics inverse solution equation can be obtained according to the structure of the lifting and turning mechanism:
[0121]
[0122] In the formula, z i (i=1,2), β i (i=1, 2) are respectively figure 1 The z-...
PUM
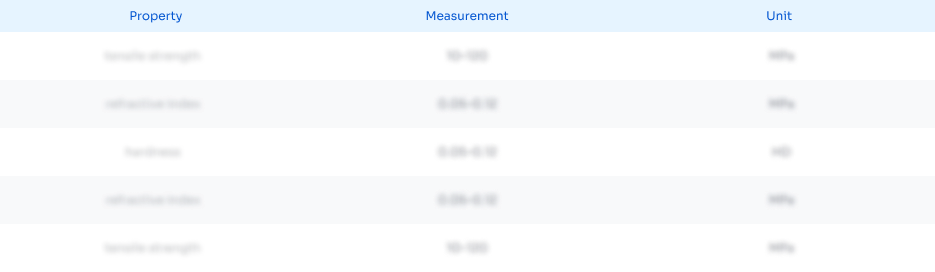
Abstract
Description
Claims
Application Information

- R&D
- Intellectual Property
- Life Sciences
- Materials
- Tech Scout
- Unparalleled Data Quality
- Higher Quality Content
- 60% Fewer Hallucinations
Browse by: Latest US Patents, China's latest patents, Technical Efficacy Thesaurus, Application Domain, Technology Topic, Popular Technical Reports.
© 2025 PatSnap. All rights reserved.Legal|Privacy policy|Modern Slavery Act Transparency Statement|Sitemap|About US| Contact US: help@patsnap.com