Process for preparing unsaturated nitrile
A technology of acrylonitrile and methacrylonitrile, applied in chemical instruments and methods, hydrocarbon ammoxidation preparation, metal/metal oxide/metal hydroxide catalysts, etc., can solve problems such as impossible and difficult maintenance, and achieve economical significant effect
- Summary
- Abstract
- Description
- Claims
- Application Information
AI Technical Summary
Problems solved by technology
Method used
Examples
Embodiment 1
[0050] Embodiment 1 (the present invention)
[0051] Composed of Mo 12.0 Bi 0.20 Ce 0.40 Fe 2.0 Ni 5.6 Mg 2.2 K 0.07 Cs 0.04 A catalyst consisting of oxide supported on 50% by weight silica was prepared as follows. In this catalyst, x is 10.7 and the ratio y of molybdenum atoms is 1.12x.
[0052] to contain SiO 2 Be that a solution is added in the 3333.4g silica sol of 30% by weight, and this solution is made of 38.6g bismuth nitrate [Bi(NO 3 ) 3 5H2O], 69.0g cerium nitrate [Ce(NO 3 ) 3 6H2O], 321.2g iron nitrate [Fe(NO 3 ) 3 9H2O], 647.6g nickel nitrate [Ni(NO 3 ) 2 6H2O], 224.2g magnesium nitrate [Mg(NO 3 ) 2 6H2O], 2.82g potassium nitrate [K(NO 3 )] and 3.10g cesium nitrate [Cs(NO 3 )] dissolved in 755.4g concentration by weight of 17.9% nitric acid and formed, finally added by 842.4g ammonium paramolybdate [(NH 4 ) 6 Mo 7 o 24 4H 2 O] dissolved in 1696.6g of water to form a solution. The resulting mixed solution was sent to a co-current type spray...
Embodiment 2
[0061] Embodiment 2 (the present invention)
[0062] The catalyst is prepared in the same manner as in Example 1, except that the composition of the oxide is Mo 11.8 Bi 0.45 Ce 0.90 Fe 1.8 Ni 5.0 Mg 2.0 K 0.09 Rb 0.05 , The calcination process is calcination at 610°C for 2 hours. In this catalyst, x is 10.8 and the ratio y of molybdenum atoms is 1.09x.
[0063] Using this catalyst, the ammoxidation of propylene was carried out under the same normal reaction conditions as in Example 1, except that the contact time was 6.7 sec.g / ml. After about 100 hours of reaction, the conversion was 99.6%, and the yield of acrylonitrile was 81.8%. The ratio of molybdenum atoms in the catalyst sampled from the reactor was 11.8 (y=1.09x).
[0064] Then the reaction was run for two weeks under the same harsh reaction conditions as in Example 1, and then returned to the original normal reaction conditions. Analysis of the reaction gas showed that the conversion rate was 99.3% and the y...
Embodiment 3
[0069] From these results, it can be seen that by adding an activator to the reaction system, the yield of acrylonitrile can be increased without increasing the molar ratio of ammonia / propylene in the feed gas, and the yield of acrylonitrile can also be obtained than that of the same molybdenum atom without adding the additive. The ratio is higher acrylonitrile yield of the catalyst, and this high acrylonitrile yield can be maintained stably. Also, since no white particles were observed in the sampled catalyst, this indicated that the added activator was actually acting as a catalyst with little deposition on the internal structure of the reactor, etc. Embodiment 3 (the present invention)
[0070] The catalyst is prepared in the same manner as in Example 1, except that the composition of the oxide is Mo 11.4 Bi 0.60 Ce 1.20 Fe 1.6 Ni 4.8 Mg 1.9 K 0.11 Rb 0.05 , The calcination process is calcination at 600°C for 2 hours. In this catalyst, x is 11.0 and the ratio y of ...
PUM
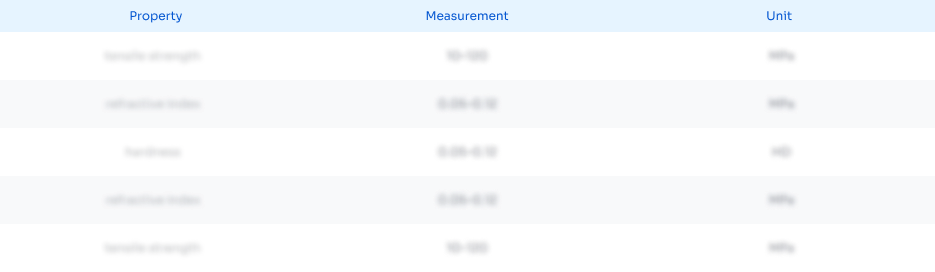
Abstract
Description
Claims
Application Information

- R&D
- Intellectual Property
- Life Sciences
- Materials
- Tech Scout
- Unparalleled Data Quality
- Higher Quality Content
- 60% Fewer Hallucinations
Browse by: Latest US Patents, China's latest patents, Technical Efficacy Thesaurus, Application Domain, Technology Topic, Popular Technical Reports.
© 2025 PatSnap. All rights reserved.Legal|Privacy policy|Modern Slavery Act Transparency Statement|Sitemap|About US| Contact US: help@patsnap.com