Automatic taking out and burying equipment for special-shaped part injection molding
A technology for injection molding and special-shaped parts, which is applied in the direction of coating, etc., can solve the problems of low effect, affect the molding efficiency, and the lack of gripping effect of special-shaped material parts, so as to achieve the effect of ensuring stability
- Summary
- Abstract
- Description
- Claims
- Application Information
AI Technical Summary
Problems solved by technology
Method used
Image
Examples
Embodiment Construction
[0032] Below in conjunction with accompanying drawing and embodiment of description, specific embodiment of the present invention is described in further detail:
[0033] refer to Figure 1 to Figure 6 The shown automatic embedding equipment for injection molding of special-shaped parts includes a transfer table 1, an injection molding machine 1a, and a top beam frame 2 erected above the injection molding machine 1a. The transfer table 1 is set up around the injection molding machine 1a, and the embedding equipment It includes a turning mechanism, a lifting mechanism, and a first servo electric cylinder 5 arranged on the upper surface of the top beam frame 2. The top beam frame 2 is provided with a sliding beam 2b that is in right angle with it. Movably matched, and can reciprocate between the injection molding machine 1a and the turntable 1 through the first servo electric cylinder 5, the lifting mechanism can be set at the other end of the sliding beam 2b through the second ...
PUM
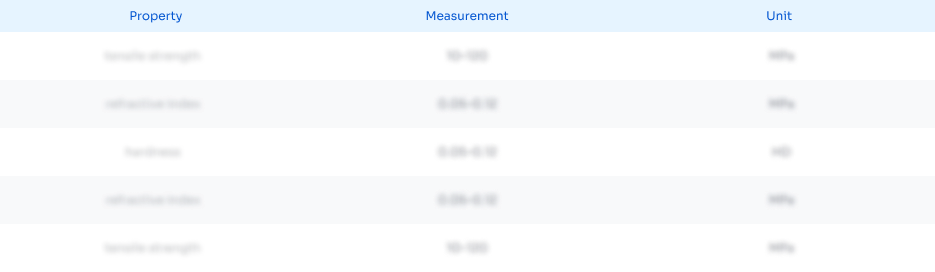
Abstract
Description
Claims
Application Information

- R&D
- Intellectual Property
- Life Sciences
- Materials
- Tech Scout
- Unparalleled Data Quality
- Higher Quality Content
- 60% Fewer Hallucinations
Browse by: Latest US Patents, China's latest patents, Technical Efficacy Thesaurus, Application Domain, Technology Topic, Popular Technical Reports.
© 2025 PatSnap. All rights reserved.Legal|Privacy policy|Modern Slavery Act Transparency Statement|Sitemap|About US| Contact US: help@patsnap.com