Wet clutch friction plate convection heat exchange coefficient mathematical model construction method
A wet clutch, convective heat exchange technology, applied in the fields of electrical digital data processing, instruments, special data processing applications, etc., can solve the problems of multiple shapes, irregularities of oil grooves, and complex structure of clutch friction plates, and achieve the effect of improving accuracy
- Summary
- Abstract
- Description
- Claims
- Application Information
AI Technical Summary
Problems solved by technology
Method used
Image
Examples
Embodiment Construction
[0034] In order to make the technical means, creative features, goals and effects of the present invention easy to understand, the following embodiments will specifically illustrate a method for constructing a wet clutch friction plate convective heat transfer coefficient mathematical model of the present invention in conjunction with the accompanying drawings.
[0035] Such as figure 1 As shown, a wet clutch friction plate convective heat transfer coefficient mathematical model construction method S100, the wet clutch is a clutch that uses cooling oil to cool down the clutch friction plate during the clutch engagement process, and is characterized in that it includes the following steps:
[0036] Step S1: Establish the slip friction work expression (1) for the clutch during the clutch engagement process,
[0037]
[0038] Among them, W is the total sliding work; T cl transmits maximum torque to the clutch, μ is the friction coefficient, n is the engine speed; R 0 , R ...
PUM
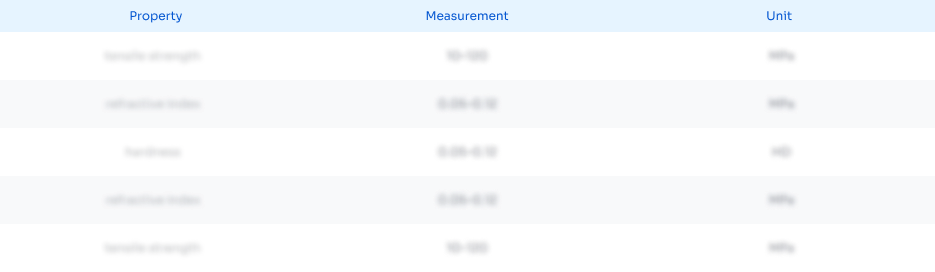
Abstract
Description
Claims
Application Information

- Generate Ideas
- Intellectual Property
- Life Sciences
- Materials
- Tech Scout
- Unparalleled Data Quality
- Higher Quality Content
- 60% Fewer Hallucinations
Browse by: Latest US Patents, China's latest patents, Technical Efficacy Thesaurus, Application Domain, Technology Topic, Popular Technical Reports.
© 2025 PatSnap. All rights reserved.Legal|Privacy policy|Modern Slavery Act Transparency Statement|Sitemap|About US| Contact US: help@patsnap.com