Gear clearance adjusting structure and robot
A gear gap and structure adjustment technology, which is applied to belts/chains/gears, mechanical equipment, transmission parts, etc., can solve the problems of difficult gear processing, high processing and assembly costs, and achieve motor damage avoidance, simple structure, and reduced The effect of manufacturing costs
- Summary
- Abstract
- Description
- Claims
- Application Information
AI Technical Summary
Problems solved by technology
Method used
Image
Examples
Embodiment 1
[0030] Embodiment 1 adopts the mode that screw rod and nut are connected
[0031] combine figure 1 As shown, the first adjustable screw 6 passes through the first gear 1 and the output shaft 5 in the axial direction and is fixed by the first nut 7, and the first adjustable screw 6 is changed by tightening or loosening the first nut 7. The position of a nut 7 on the first adjustable screw rod 6 makes the first gear 1 shift under the elastic force of the first compression spring 3, that is, stretch out or retreat, thereby changing the gear clearance, specifically, tighten the first gear 1 When tightening the nut 7, the distance between the first nut 7 and the end of the first adjustable screw rod 6 decreases, so that the first gear 1 will retreat toward the direction away from the second gear 2, so that the gear gap becomes larger, otherwise, when the screw is loosened When the first nut 7, the distance between the first nut 7 and the end of the first adjustable screw 6 becomes...
Embodiment 2
[0035] Embodiment 2 adopts screw rod and threaded connection
[0036]The first adjustable screw 6 is threadedly connected to the first gear 1, and the second adjustable screw 17 is threaded to the second gear 2. Specifically, the first gear 1 and the second gear 2 are axially provided with a plurality of threaded holes matching the screw rod. Here, for the convenience of explanation, the gears are used instead of the first gear 1 or the second gear 2. The gear clearance adjustment structure is also provided with a mounting flange. Both the first gear assembly and the second gear assembly are provided, the compression spring is arranged between the gear and the mounting flange, the screw rod passes through the mounting flange and is threadedly connected with the threaded hole of the gear, and the depth screwed into the threaded hole by adjusting the screw rod can be adjusted. Adjust the distance between the gear and the mounting flange so that the clearance of the gear can be c...
PUM
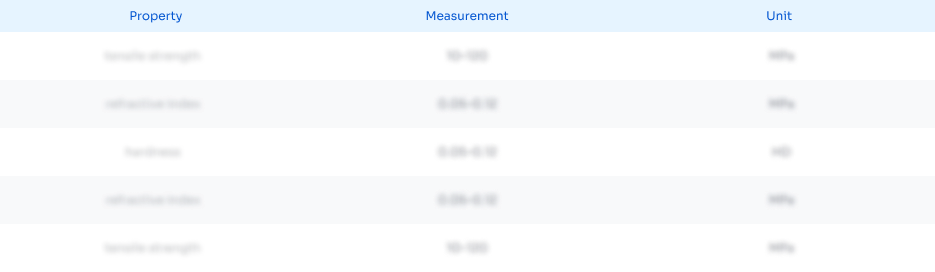
Abstract
Description
Claims
Application Information

- R&D Engineer
- R&D Manager
- IP Professional
- Industry Leading Data Capabilities
- Powerful AI technology
- Patent DNA Extraction
Browse by: Latest US Patents, China's latest patents, Technical Efficacy Thesaurus, Application Domain, Technology Topic, Popular Technical Reports.
© 2024 PatSnap. All rights reserved.Legal|Privacy policy|Modern Slavery Act Transparency Statement|Sitemap|About US| Contact US: help@patsnap.com