A rotary robot joint
A robot joint and robot technology, applied in the field of robotics, can solve problems such as large restrictions on the effective rotation angle of robot joints, restrictions on the range of swing angles, and large internal leakage.
- Summary
- Abstract
- Description
- Claims
- Application Information
AI Technical Summary
Problems solved by technology
Method used
Image
Examples
Embodiment Construction
[0019] The following will clearly and completely describe the technical solutions in the embodiments of the present invention with reference to the accompanying drawings in the embodiments of the present invention. Obviously, the embodiments described below are some, not all, embodiments of the present invention. Based on the embodiments of the present invention, all other embodiments obtained by persons of ordinary skill in the art without making creative efforts belong to the protection scope of the present invention.
[0020] combine figure 1 and figure 2 As shown, a rotary robot joint includes a robot arm 8, a robot arm 3, a double-piston rod hydraulic cylinder A and a rotary motion mechanism B;
[0021] The robot arm 8 is a hollow arm, and the double piston rod hydraulic cylinder A and the rotary motion mechanism B are arranged in the robot arm 8. The hydraulic cylinder body 16 of the double piston rod hydraulic cylinder A is connected with the rotary motion mechanism B...
PUM
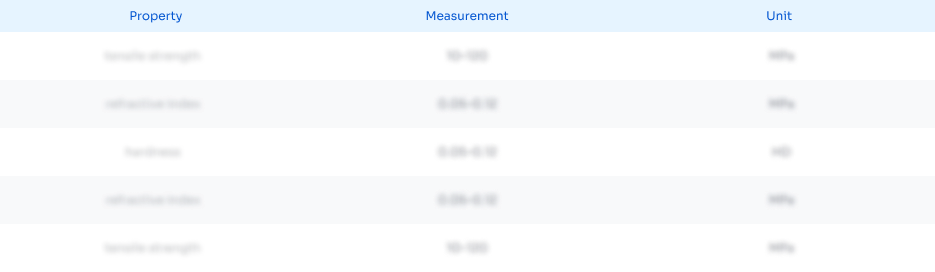
Abstract
Description
Claims
Application Information

- R&D
- Intellectual Property
- Life Sciences
- Materials
- Tech Scout
- Unparalleled Data Quality
- Higher Quality Content
- 60% Fewer Hallucinations
Browse by: Latest US Patents, China's latest patents, Technical Efficacy Thesaurus, Application Domain, Technology Topic, Popular Technical Reports.
© 2025 PatSnap. All rights reserved.Legal|Privacy policy|Modern Slavery Act Transparency Statement|Sitemap|About US| Contact US: help@patsnap.com