Electro-hydraulic control system, method and device
An electro-hydraulic control system and electro-hydraulic control technology are applied in fluid pressure actuation devices, fluid pressure actuation system components, servo meter circuits, etc., and can solve the displacement error detected by the displacement sensor 7, large displacement response fluctuations, Unable to accurately realize the pitch change of wind turbines and other issues, to achieve the effect of reducing displacement deviation, improving correction accuracy, and reducing influencing factors
- Summary
- Abstract
- Description
- Claims
- Application Information
AI Technical Summary
Problems solved by technology
Method used
Image
Examples
Embodiment Construction
[0029] The present invention may have various modifications and various embodiments, and it should be understood that the present invention is not limited to these embodiments, but includes all modifications, equivalents and replacements within the spirit and scope of the present invention.
[0030] In the present invention, expressions including ordinal numbers such as "first" and "second" can modify various elements. However, these elements are not limited by such expressions. A first element could be termed a second element, and, similarly, a second element could be termed a first element, without departing from the scope of example embodiments of the present invention.
[0031] The terms used in the example embodiments of the present invention are for describing specific embodiments only, and are not intended to limit the example embodiments. As used herein, the singular forms are intended to include the plural forms as well, unless the context clearly dictates otherwise....
PUM
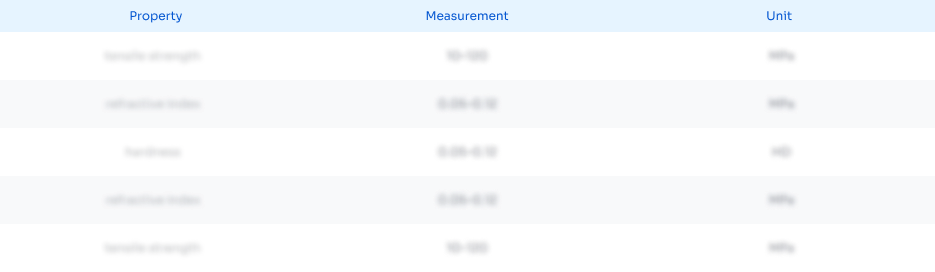
Abstract
Description
Claims
Application Information

- R&D
- Intellectual Property
- Life Sciences
- Materials
- Tech Scout
- Unparalleled Data Quality
- Higher Quality Content
- 60% Fewer Hallucinations
Browse by: Latest US Patents, China's latest patents, Technical Efficacy Thesaurus, Application Domain, Technology Topic, Popular Technical Reports.
© 2025 PatSnap. All rights reserved.Legal|Privacy policy|Modern Slavery Act Transparency Statement|Sitemap|About US| Contact US: help@patsnap.com