a rh jet co 2 Dynamic control method for refining ultra-low carbon steel
A dynamic control, ultra-low carbon steel technology, applied in the field of steelmaking technology, can solve the problems of large consumption of deoxidized alloy, easy peroxidation of molten steel, high production cost, etc., to shorten the refining rhythm, improve the quality of molten steel, and improve the quality of molten steel quality effect
- Summary
- Abstract
- Description
- Claims
- Application Information
AI Technical Summary
Problems solved by technology
Method used
Image
Examples
Embodiment 1
[0020] Embodiment 1: the present invention is applied in the 150tRH refining process, and the top blowing gas is O 2 +CO 2 , the lifting gas is Ar+CO 2 , the deoxidizer adopts aluminum block alloy, and the alloy yield is 80%. Specific steps are as follows:
[0021] 1): Quickly measure the carbon content of RH incoming molten steel through the RH incoming molten steel composition data acquisition system [%C] 0 =0.038%, and transmit it to the central control system, and formulate the operation process of the forced decarburization period according to the target composition data of molten steel.
[0022] 2): During the forced decarburization period, according to the operation process established in step 1, under the ultimate vacuum, use top blown O 2 +CO 2 Carry out forced decarburization with Ar+CO 2 In order to enhance the circulating stirring of molten pool by lifting gas, predict the carbon content of molten steel at the end of decarburization [%C] f , and at the end of ...
Embodiment 2
[0027] Embodiment 2: the present invention is applied in the 300t RH refining process, and the top blowing gas is O 2 +CO 2 , the lifting gas is Ar+CO 2 , the deoxidizer adopts aluminum block alloy, and the alloy yield is 75%. Specific steps are as follows:
[0028] 1): Quickly measure the carbon content of RH incoming molten steel through the RH incoming molten steel composition data acquisition system [%C] 0 =0.035%, and transmit it to the central control system, and formulate the operation process of the forced decarburization period according to the target composition data of molten steel.
[0029] 2): During the forced decarburization period, according to the operation process established in step 1, under the ultimate vacuum, use top blown O 2 +CO 2 Carry out forced decarburization with Ar+CO 2 In order to enhance the circulating stirring of molten pool by lifting gas, predict the carbon content of molten steel at the end of decarburization [%C] f , and at the end ...
PUM
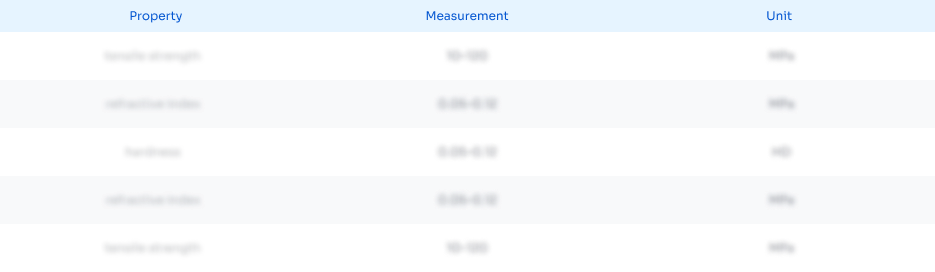
Abstract
Description
Claims
Application Information

- Generate Ideas
- Intellectual Property
- Life Sciences
- Materials
- Tech Scout
- Unparalleled Data Quality
- Higher Quality Content
- 60% Fewer Hallucinations
Browse by: Latest US Patents, China's latest patents, Technical Efficacy Thesaurus, Application Domain, Technology Topic, Popular Technical Reports.
© 2025 PatSnap. All rights reserved.Legal|Privacy policy|Modern Slavery Act Transparency Statement|Sitemap|About US| Contact US: help@patsnap.com