Model-free current predictive control method and control system for SMPMSM drive system with online optimization of inverter reference voltage vector
A technology of reference voltage vector and drive system, applied in vector control system, motor generator control, control system and other directions, can solve the problem of insufficient current control method of SMPMSM drive system
- Summary
- Abstract
- Description
- Claims
- Application Information
AI Technical Summary
Problems solved by technology
Method used
Image
Examples
Embodiment Construction
[0090] In order to have a further understanding and understanding of the structural features of the present invention and the achieved effects, the preferred embodiments and accompanying drawings are used for a detailed description, as follows:
[0091] Such as figure 2 As shown, the control system of the SMPMSM drive system model-free current predictive control method of an inverter reference voltage vector online optimization according to the present invention comprises a DC power supply according to the traditional method of the prior art, and the output of the DC power supply The terminal is connected with an inverter and a voltage sensor, the output end of the inverter is connected with a current sensor and a permanent magnet synchronous motor, and a position sensor is installed on the permanent magnet synchronous motor.
[0092] Current predictive control DSP is used to directly establish the relationship between inverter reference voltage vector phase, amplitude and co...
PUM
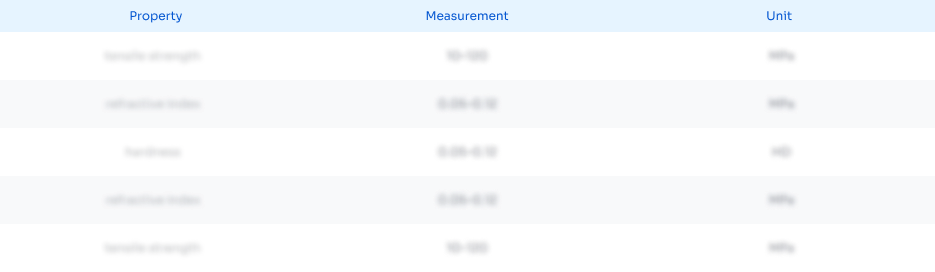
Abstract
Description
Claims
Application Information

- R&D Engineer
- R&D Manager
- IP Professional
- Industry Leading Data Capabilities
- Powerful AI technology
- Patent DNA Extraction
Browse by: Latest US Patents, China's latest patents, Technical Efficacy Thesaurus, Application Domain, Technology Topic, Popular Technical Reports.
© 2024 PatSnap. All rights reserved.Legal|Privacy policy|Modern Slavery Act Transparency Statement|Sitemap|About US| Contact US: help@patsnap.com