Aftertreatment technology of hydantion serialization preparation of glycine
A technology of glycine and Heine method, which is applied in the post-treatment field of continuous preparation of glycine by Hein method, can solve the problems of consuming raw steam, affecting the quality and yield of glycine, etc., and achieve the effect of improving product purity
- Summary
- Abstract
- Description
- Claims
- Application Information
AI Technical Summary
Problems solved by technology
Method used
Image
Examples
Embodiment 1
[0044] The glycine aqueous solution prepared continuously by hydantoin method is as follows: 3.85wt% glycine, 1.21wt% hydantoin, 0.11wt% hydantoin, 0.05wt% hydantoin amide, 0.03wt% 2,5-diketopiperazine, Glycinamide 0.06 wt%.
[0045] Post-process as follows:
[0046] The glycine aqueous solution was transported to the MVR, the evaporation temperature was 60° C., the time was 2.5 h, and the evaporation was concentrated under vacuum conditions. The concentrated solution is sent to the crystallization kettle, the crystallization temperature is 15°C, the rotation speed is 25r / min, after cooling down for 2.5h, the centrifuge is centrifuged at 1000r / min until no liquid flows out. Dissolve glycine crystals in deionized water at a ratio of 40g / 100mL, add 0.5% activated carbon (based on the mass of glycine), heat up to 70°C, and stir at 35r / min for 0.5h. After filtration, the filtrate was poured into a recrystallization kettle, and recrystallized at 10°C and 20r / min for 3h. Then, ce...
Embodiment 2
[0048] The glycine aqueous solution prepared continuously by hydantoin method is as follows: 3.85wt% glycine, 1.21wt% hydantoin, 0.11wt% hydantoin, 0.05wt% hydantoin amide, 0.03wt% 2,5-diketopiperazine, Glycinamide 0.06 wt%.
[0049] Post-process as follows:
[0050] The glycine aqueous solution was transported to the MVR, the evaporation temperature was 70° C., the time was 2 hours, and the evaporation and concentration were carried out under vacuum conditions. The concentrated solution is sent to the crystallization tank, the crystallization temperature is 15°C, the rotation speed is 30r / min, after cooling down for 2 hours, it is centrifuged in the centrifuge at 1000r / min until no liquid flows out. Dissolve glycine crystals in deionized water at a ratio of 40g / 100mL, add 1% activated carbon (according to the mass of glycine), raise the temperature to 75°C, and stir at 60r / min for 0.5h. After filtration, the filtrate was poured into a recrystallization kettle, and recrystal...
Embodiment 3
[0052] The glycine aqueous solution prepared continuously by hydantoin method is as follows: 3.85wt% glycine, 1.21wt% hydantoin, 0.11wt% hydantoin, 0.05wt% hydantoin amide, 0.03wt% 2,5-diketopiperazine, Glycinamide 0.06 wt%.
[0053] Post-process as follows:
[0054] The glycine aqueous solution was transported to the MVR, the evaporation temperature was 70° C., the time was 2 hours, and the evaporation and concentration were carried out under vacuum conditions. The concentrated solution is sent to the crystallization kettle, the crystallization temperature is 15°C, the rotation speed is 25r / min, after cooling down for 2.5h, the centrifuge is centrifuged at 1000r / min until no liquid flows out. Dissolve glycine crystals in deionized water at a ratio of 45g / 100mL, add 0.8% activated carbon (according to the mass of glycine), heat up to 80°C, and stir at 45r / min for 0.5h. After filtration, the filtrate was poured into a recrystallization kettle, and recrystallized at 10°C and 3...
PUM
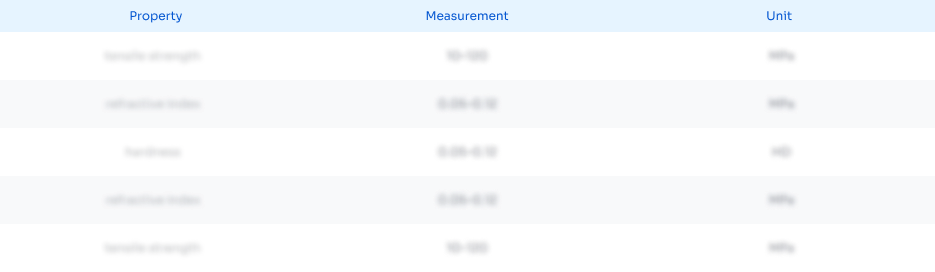
Abstract
Description
Claims
Application Information

- R&D Engineer
- R&D Manager
- IP Professional
- Industry Leading Data Capabilities
- Powerful AI technology
- Patent DNA Extraction
Browse by: Latest US Patents, China's latest patents, Technical Efficacy Thesaurus, Application Domain, Technology Topic, Popular Technical Reports.
© 2024 PatSnap. All rights reserved.Legal|Privacy policy|Modern Slavery Act Transparency Statement|Sitemap|About US| Contact US: help@patsnap.com