Pd redispersed Pd/MCx supported catalyst and preparation method and application thereof
A supported catalyst and catalyst technology, applied in the direction of physical/chemical process catalysts, dehalogenation preparation, chemical instruments and methods, etc., can solve the problems of unenvironmental protection, unsatisfactory recovery of catalyst activity, low efficiency, etc., and achieve low production costs , excellent selectivity, simple preparation method
- Summary
- Abstract
- Description
- Claims
- Application Information
AI Technical Summary
Problems solved by technology
Method used
Image
Examples
Embodiment 1
[0025] 1 g of fresh Pd / FeC with a Pd loading of 3% x The catalyst was loaded into a fixed-bed reactor, fed with hydrogen and reduced at 250°C for 2 hours. Then feed CFC-115 gas at a reaction temperature of 300°C and a space velocity of 720h -1 The reaction is carried out under the conditions, and the feed molar ratio of CFC-115 raw material to hydrogen is 1:1.5. After 80 hours of reaction, when the conversion rate of CFC-115 is lower than 65%, it is recorded as the sintering deactivation of the catalyst.
[0026] The catalyst deactivated by sintering in O with an oxygen volume content of 8% 2 / N 2 Pd / FeO was obtained by calcination at 450℃ for 0.5h x catalyst, and then 10% CH at 300°C 4 / H 2 Gas mixture (i.e. CH 4 / H 2 In the gas mixture, CH 4 The volume content is 10%) calcined and carbonized for 1h to recover Pd / FeC x The activity of the catalyst, that is, the regenerated catalyst is obtained. Under the same reaction conditions, the hydrodechlorination reaction of...
Embodiment 2
[0029] 1 g of fresh Pd / FeC with a Pd loading of 9% x The catalyst was loaded into a fixed-bed reactor, fed with hydrogen and reduced at 250°C for 2 hours. Then feed CFC-115 gas at a reaction temperature of 300°C and a space velocity of 720h -1 The reaction is carried out under the conditions, and the feed molar ratio of CFC-115 raw material to hydrogen is 1:1.5. After 80 hours of reaction, when the conversion rate of CFC-115 is lower than 65%, it is recorded as the sintering deactivation of the catalyst.
[0030] The catalyst deactivated by sintering in O with an oxygen volume content of 16% 2 / N 2atmosphere and calcination at 400°C for 8h to obtain Pd / FeO x catalyst, and then 20% CH at 650°C 4 / H 2 Restoration of Pd / FeC by Mixed Gas Calcination and Carbonization for 10h x The activity of the catalyst, that is, the regenerated catalyst is obtained. Under the same conditions, the hydrodechlorination reaction of CFC-115 under the action of the regenerated catalyst was ca...
Embodiment 3
[0033] 1 g of fresh Pd / FeC with a Pd loading of 5% x The catalyst was loaded into a fixed-bed reactor, fed with hydrogen and reduced at 250°C for 2 hours. Then feed CFC-115 gas at a reaction temperature of 300°C and a space velocity of 720h -1 The reaction is carried out under the conditions, and the feed molar ratio of CFC-115 raw material to hydrogen is 1:1.5. After 80 hours of reaction, when the conversion rate of CFC-115 is lower than 65%, it is recorded as the sintering deactivation of the catalyst.
[0034] The catalyst deactivated by sintering in O with an oxygen volume content of 6% 2 / N 2 atmosphere and calcination at 500°C for 1 h to obtain Pd / FeO x Catalyst, and then calcination and carbonization at 300 °C for 3 h to recover Pd / FeC x The activity of the catalyst, that is, the regenerated catalyst is obtained. Under the same conditions, the hydrodechlorination reaction of CFC-115 under the action of the regenerated catalyst was carried out again.
[0035] When...
PUM
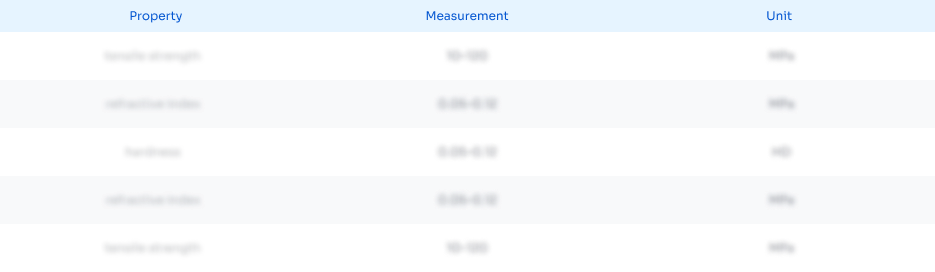
Abstract
Description
Claims
Application Information

- R&D Engineer
- R&D Manager
- IP Professional
- Industry Leading Data Capabilities
- Powerful AI technology
- Patent DNA Extraction
Browse by: Latest US Patents, China's latest patents, Technical Efficacy Thesaurus, Application Domain, Technology Topic, Popular Technical Reports.
© 2024 PatSnap. All rights reserved.Legal|Privacy policy|Modern Slavery Act Transparency Statement|Sitemap|About US| Contact US: help@patsnap.com