Purification and separation integrated device for polymer
A technology of purification, separation and polymer, applied in the direction of filtration separation, separation method, fractionation, etc., which can solve the problems of increasing the loss of poor solvents, difficulty in filtration, and a large number of equipment
- Summary
- Abstract
- Description
- Claims
- Application Information
AI Technical Summary
Problems solved by technology
Method used
Image
Examples
Embodiment 1
[0122] Such as figure 1 As shown, this embodiment provides an integrated polymer purification and separation device, including a liquid polymer tank 1, a receiving tank 2, a poor solvent tank 3, a fluidized bed 4, a rectification tower 5 and a PLC control system;
[0123] The cylinder body of the fluidized bed 4 is a conical structure, and the upper cover of the fluidized bed 4 is provided with a granular polymer feed port 41, a liquid polymer feed port 42 and a riser pipe 43, and the riser pipe 43 communicates with the fluidized bed 4 and a rectification tower 5, the rectification tower 5 is placed above the fluidized bed 4; the inside of the upper cover of the fluidized bed 4 is provided with a filter 44; Mirror 45; the bottom of the fluidized bed 4 is provided with a filter plate 46, the bottom of the filter plate 46 is provided with a liquid circulation pump 47, and the fluidized bed 4 is provided with a product discharge port 48 at the cylinder above the filter plate 46, ...
PUM
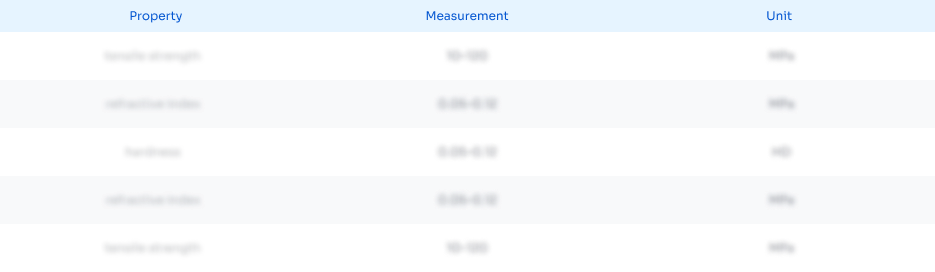
Abstract
Description
Claims
Application Information

- R&D Engineer
- R&D Manager
- IP Professional
- Industry Leading Data Capabilities
- Powerful AI technology
- Patent DNA Extraction
Browse by: Latest US Patents, China's latest patents, Technical Efficacy Thesaurus, Application Domain, Technology Topic, Popular Technical Reports.
© 2024 PatSnap. All rights reserved.Legal|Privacy policy|Modern Slavery Act Transparency Statement|Sitemap|About US| Contact US: help@patsnap.com