PE (polyethylene) sheath material and preparation method thereof
A sheathing material, polymethyl methacrylate technology, applied in plastic/resin/wax insulators, organic insulators, etc., can solve the problems of poor resistance to low temperature shock embrittlement, poor ability to withstand external forces, affecting service life, etc. Achieve the effect of improving mechanical properties, ensuring processing performance, and improving cable life
- Summary
- Abstract
- Description
- Claims
- Application Information
AI Technical Summary
Problems solved by technology
Method used
Image
Examples
Embodiment 1
[0020] A preparation method of PE sheath material, wherein, its preparation method is as follows:
[0021] (1) Add alkali-free glass fiber, polymethyl methacrylate, nano-alumina and polyacrylonitrile in a high-speed mixer and stir and mix evenly at 85°C to obtain a filler;
[0022] The alkali-free glass fiber, polymethyl methacrylate, nano-alumina and polyacrylonitrile are mixed according to the mass ratio of 3:3:2:1;
[0023] (2) Take 29 parts of filler and 16 parts of compatibilizer according to the mass fraction, place them in a double-roller mixer, and mix them at 175°C for 25 minutes;
[0024] The compatibilizer is a mixture of maleic anhydride grafted EPDM, titanate coupling agent 201, and glycidyl methacrylate. The maleic anhydride grafted EPDM, titanate coupling agent 201, methyl Glycidyl acrylate is mixed according to the mass ratio of 3:7:2;
[0025] Then add 62 parts of high-density polyethylene and 39 parts of linear low-density polyethylene successively, heat up...
Embodiment 2
[0030] A preparation method of PE sheath material, wherein, its preparation method is as follows:
[0031] (1) Add polymethyl methacrylate and polyacrylonitrile in sequence in a high mixer and stir and mix evenly at 80-95°C to obtain a filler; the polymethyl methacrylate and polyacrylonitrile are mixed according to the mass ratio 6:1;
[0032] (2) Take 35 parts of filler and 18 parts of compatibilizer according to the mass fraction, place them in a double-roller mixer, and knead for 23 minutes at 168 ° C. The compatibilizer is maleic anhydride grafted EPDM, methacrylic acid Glycidyl esters are mixed, and the maleic anhydride grafted EPDM and glycidyl methacrylate are mixed according to the mass ratio of 3:7;
[0033] Then add 59 parts of high-density polyethylene and 40 parts of linear low-density polyethylene successively, heat up to 198°C and mix for 1 hour, then add 5 parts of anti-aging agent and 3 parts of processing aid and mix for 12 minutes to obtain a mixture;
[00...
Embodiment 3
[0038] A preparation method of PE sheath material, wherein, its preparation method is as follows:
[0039] (1) Add alkali-free glass fiber, polymethyl methacrylate, and nano-alumina in a high-speed mixer in sequence, and stir and mix evenly at 80-95°C to obtain fillers;
[0040] The alkali-free glass fiber, polymethyl methacrylate, and nano-alumina are mixed according to the mass ratio of 4:4:5;
[0041] (2) Take 36 parts of filler and 17 parts of compatibilizer according to the mass fraction, place them in a double-roller mixer, and knead at 175 ° C for 28 minutes. The compatibilizer is maleic anhydride grafted EPDM, titanate The coupling agent 201 is mixed, and the maleic anhydride grafted EPDM and the titanate coupling agent 201 are mixed according to the mass ratio of 3:8;
[0042] Then add 52 parts of high-density polyethylene and 33 parts of linear low-density polyethylene successively, heat up to 208°C and knead for 1.8 hours, then add 7 parts of anti-aging agent and 2...
PUM
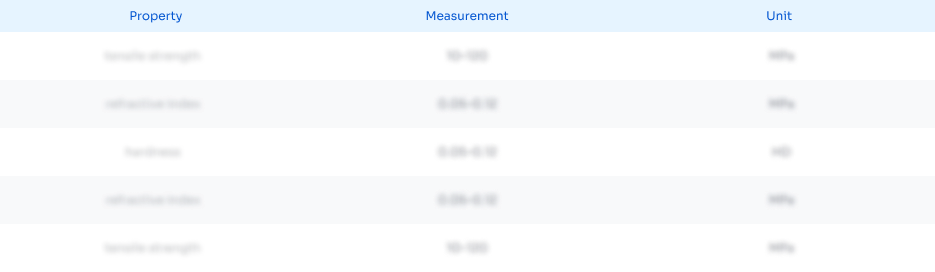
Abstract
Description
Claims
Application Information

- R&D Engineer
- R&D Manager
- IP Professional
- Industry Leading Data Capabilities
- Powerful AI technology
- Patent DNA Extraction
Browse by: Latest US Patents, China's latest patents, Technical Efficacy Thesaurus, Application Domain, Technology Topic, Popular Technical Reports.
© 2024 PatSnap. All rights reserved.Legal|Privacy policy|Modern Slavery Act Transparency Statement|Sitemap|About US| Contact US: help@patsnap.com