Heatproof, transparent and impact-resistant PVDF/PP alloy material and preparation method thereof
An alloy material, transparent technology, applied in the field of materials, can solve the problems of large molding shrinkage, insufficient wear resistance, low heat distortion temperature, etc.
- Summary
- Abstract
- Description
- Claims
- Application Information
AI Technical Summary
Problems solved by technology
Method used
Image
Examples
Embodiment 1
[0035] A heat-resistant transparent impact-resistant PVDF / PP alloy material is modified by blending PP, solubilizer, inorganic mineral powder and transparent nucleating agent, and then the modified PP, PVDF and solubilizer are blended to obtain mixture of materials.
[0036] A preparation method of a heat-resistant transparent impact-resistant PVDF / PP alloy material, comprising the following steps:
[0037] S1. Extrude talcum powder (2500ppm), diatomaceous earth and compatibilizer (8%) with surface pretreatment, and a small amount of copolymerized PP on a twin-screw extruder to form a high-concentration masterbatch, and then blend the masterbatch with PP , prepare modified PP material;
[0038] S2. Weigh the PVDF material (content 20%) and the modified PP material in proportion, and put them into a Haake rotor rheometer for mixing at a temperature of 150° C. for 15 minutes;
[0039] S3. After the mixing is completed, stop the machine, discharge the material, and leave the mi...
Embodiment 2
[0044] A heat-resistant transparent impact-resistant PVDF / PP alloy material is modified by blending PP, solubilizer, inorganic mineral powder and transparent nucleating agent, and then the modified PP, PVDF and solubilizer are blended to obtain mixture of materials.
[0045] A preparation method of a heat-resistant transparent impact-resistant PVDF / PP alloy material, comprising the following steps:
[0046] S1. Extrude the pretreated calcium carbonate (1000ppm), diatomite and compatibilizer (10%) on the surface, and a small amount of copolymerized PP on a twin-screw extruder to form a high-concentration masterbatch, and then blend the masterbatch with PP , prepare modified PP material;
[0047] S2. Weigh the PVDF (35%) material and the modified PP material in proportion, and put them into a Haake rotor rheometer for mixing at a temperature of 155° C. for 18 minutes;
[0048] S3. After the mixing is completed, stop the machine, discharge the material, and leave the mixed mate...
Embodiment 3
[0053] A heat-resistant transparent impact-resistant PVDF / PP alloy material is modified by blending PP, solubilizer, inorganic mineral powder and transparent nucleating agent, and then the modified PP, PVDF and solubilizer are blended to obtain mixture of materials.
[0054] A preparation method of a heat-resistant transparent impact-resistant PVDF / PP alloy material, comprising the following steps:
[0055] S1. Extrude talcum powder (1500ppm), diatomaceous earth, compatibilizer (15%) and a small amount of copolymerized PP on a twin-screw extruder to form a high-concentration masterbatch, and then blend the masterbatch with PP , prepare modified PP material;
[0056] S2. Weigh the PVDF material (45%) and the modified PP material in proportion, and put them into a Haake rotor rheometer for mixing at a temperature of 160° C. for 20 minutes;
[0057] S3. After the mixing is completed, stop the machine, discharge the material, and leave the mixed material for 26 hours;
[0058] ...
PUM
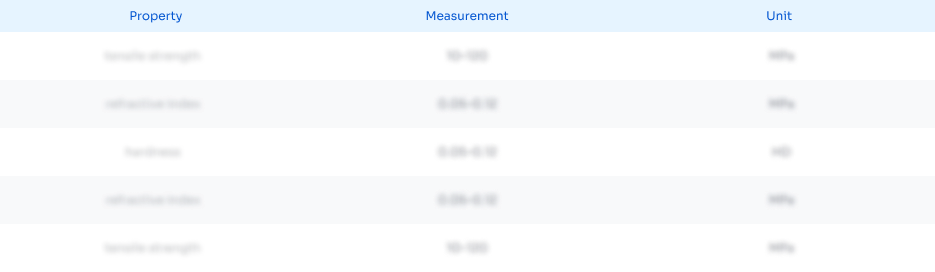
Abstract
Description
Claims
Application Information

- Generate Ideas
- Intellectual Property
- Life Sciences
- Materials
- Tech Scout
- Unparalleled Data Quality
- Higher Quality Content
- 60% Fewer Hallucinations
Browse by: Latest US Patents, China's latest patents, Technical Efficacy Thesaurus, Application Domain, Technology Topic, Popular Technical Reports.
© 2025 PatSnap. All rights reserved.Legal|Privacy policy|Modern Slavery Act Transparency Statement|Sitemap|About US| Contact US: help@patsnap.com