Powder metallurgy preparation method of double-clutch large-torque automatic gearbox synchronizer gear hub
An automatic gearbox and powder metallurgy technology, applied in the field of powder metallurgy auto parts, can solve the problems of high brush loss, affecting the precision of finished products, and slow deburring efficiency, so as to improve the tensile strength and fatigue life, and improve the tooth profile and dimensional accuracy, avoiding the effect of excessive tensile stress
- Summary
- Abstract
- Description
- Claims
- Application Information
AI Technical Summary
Problems solved by technology
Method used
Image
Examples
Embodiment 1
[0029] Embodiment 1: A powder metallurgy preparation method for a synchronizer gear hub of a dual-clutch high-torque automatic transmission includes the following steps:
[0030] (1) Mixing: Design the composition and mixing of raw materials, and mix the following raw materials uniformly by mass percentage: C: 0.7%, Cu: 1.3%; Ni: 4.5%; Mo: 0.4%, the rest is Fe and unavoidable Impurities are metallurgical raw materials.
[0031] (2) Forming: put the metallurgical raw materials obtained in step (1) into the forming machine, and press with a 500T CNC forming press, the overall density of the gear hub is 7.05g / cm 3, the density of the special-shaped keyway and the connecting rib of the gear hub body is 7.12g / cm 3 ; Segmentation density of each forming section≤0.2g / cm 3 , there are no cracks at the joints of each part of the green body. After the green body is demolded, the burr is automatically brushed to obtain the tooth hub.
[0032] (3) Pre-sintering: take the gear hub obta...
Embodiment 2
[0042] Embodiment 2: A powder metallurgy preparation method for a synchronizer gear hub of a dual-clutch high-torque automatic gearbox comprises the following steps:
[0043] (1) Mixing: Design the composition and mixing of raw materials, and mix the following raw materials uniformly by mass percentage: C: 0.5%, Cu: 1.7%; Ni: 3.5%; Mo: 0.6%%, the rest is Fe and unavoidable The impurities are obtained as powder metallurgy raw materials.
[0044] (2) Forming: put the metallurgical raw materials obtained in step (1) into the forming machine, and press with a 500T CNC forming press, the overall density of the gear hub is 7.08g / cm 3 , the density at the connecting rib between the special-shaped keyway and the gear hub body is 7.11g / cm 3 ; Segmentation density of each forming section≤0.2g / cm 3 , there are no cracks at the joints of each part of the green body. After the green body is demolded, the burr is automatically brushed to obtain the tooth hub.
[0045] (3) Pre-sintering:...
Embodiment 3
[0055] Embodiment 3: A powder metallurgy preparation method for a synchronizer gear hub of a dual-clutch high-torque automatic gearbox comprises the following steps:
[0056] (1) Mixing: Design the composition and mixing of raw materials, and mix the following raw materials uniformly by mass percentage: C: 0.6%, Cu: 1.5%; Ni: 4.0%; Mo: 0.5%, the rest is Fe and unavoidable Impurities are metallurgical raw materials.
[0057] (2) Forming: put the metallurgical raw materials obtained in step (1) into the forming machine, and press with a 500T CNC forming press, the overall density of the gear hub is 7.06g / cm 3 , the density of the special-shaped keyway and the connecting rib of the gear hub body is 7.13g / cm 3 ; Segmentation density of each forming section≤0.2g / cm 3 , there are no cracks at the joints of each part of the green body. After the green body is demolded, the burr is automatically brushed to obtain the tooth hub.
[0058] (3) Pre-sintering: take the gear hub obtaine...
PUM
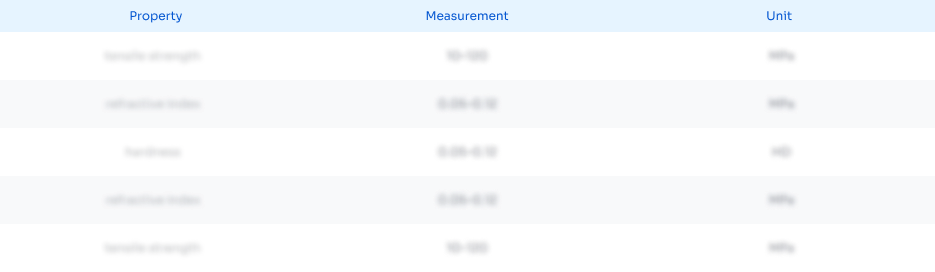
Abstract
Description
Claims
Application Information

- R&D Engineer
- R&D Manager
- IP Professional
- Industry Leading Data Capabilities
- Powerful AI technology
- Patent DNA Extraction
Browse by: Latest US Patents, China's latest patents, Technical Efficacy Thesaurus, Application Domain, Technology Topic, Popular Technical Reports.
© 2024 PatSnap. All rights reserved.Legal|Privacy policy|Modern Slavery Act Transparency Statement|Sitemap|About US| Contact US: help@patsnap.com