A multi-objective optimization design method for dynamic characteristics of a feeding system
A technology of multi-objective optimization and feeding system, which is applied in the field of multi-objective optimization design of dynamic characteristics of feeding system, and can solve the problems of inability to guarantee analysis accuracy, failure to consider the deformation of key structural parts, and long calculation time.
- Summary
- Abstract
- Description
- Claims
- Application Information
AI Technical Summary
Problems solved by technology
Method used
Image
Examples
Embodiment Construction
[0056] The present invention will be described in detail below in conjunction with the implementation drawings and accompanying drawings.
[0057] A multi-objective optimization design method for the dynamic characteristics of the feed system of the present invention, the overall flow chart is as follows figure 1 shown. Include the following steps:
[0058] Step 1. Establish a rigid-flexible-electromechanical coupling feed system dynamic characteristic simulation analysis model, including the following steps:
[0059] In the first step, the geometric parameters and material properties of the feed system ball screw are determined. The geometric parameters of the ball screw include the diameter and length of the shaft outer diameter of each optical shaft part, the nominal diameter and length of the threaded part; the material properties of the ball screw include elastic modulus, Poisson's ratio and density.
[0060] In the second step, the ball screw of the feed system is div...
PUM
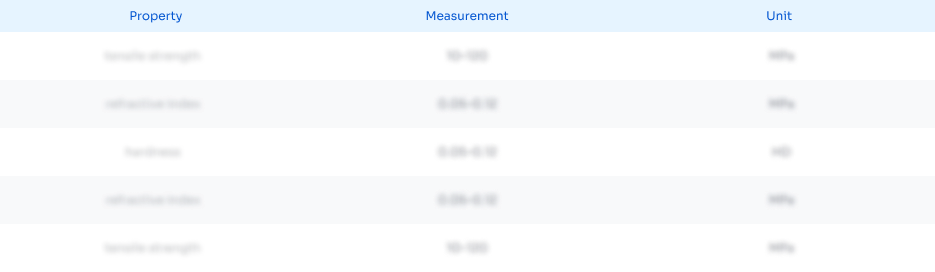
Abstract
Description
Claims
Application Information

- R&D Engineer
- R&D Manager
- IP Professional
- Industry Leading Data Capabilities
- Powerful AI technology
- Patent DNA Extraction
Browse by: Latest US Patents, China's latest patents, Technical Efficacy Thesaurus, Application Domain, Technology Topic, Popular Technical Reports.
© 2024 PatSnap. All rights reserved.Legal|Privacy policy|Modern Slavery Act Transparency Statement|Sitemap|About US| Contact US: help@patsnap.com