A method for evaluating the FOD resistance of an aero-engine blade
A technology for aero-engines and blades, applied in special data processing applications, instruments, electrical digital data processing, etc., can solve problems that cannot be effectively avoided, residual stress, large metal dispersion, etc., to achieve accurate FOD resistance, avoid The effect of blade failure
- Summary
- Abstract
- Description
- Claims
- Application Information
AI Technical Summary
Problems solved by technology
Method used
Image
Examples
Embodiment Construction
[0022] Below, the present invention will be described in further detail in conjunction with the accompanying drawings.
[0023] Such as figure 1 As shown, the present invention discloses a method for evaluating the anti-FOD capability of an aeroengine blade, comprising the following steps:
[0024] A method for evaluating the anti-FOD capability of an aeroengine blade, comprising the following steps:
[0025] (1) Analysis of blade vibration stress and static strength: use UG or other engineering modeling software to establish a numerical model of the blade, perform modal analysis on the real blade finite element model in ANSYS or other finite element analysis software, and analyze the blade finite element The model applies the same rotational speed and boundary conditions as the working load, and calculates the dynamic frequency and vibration stress distribution of the blade. Extract the position of the maximum stress on the leading edge of the blade. Because the vibration s...
PUM
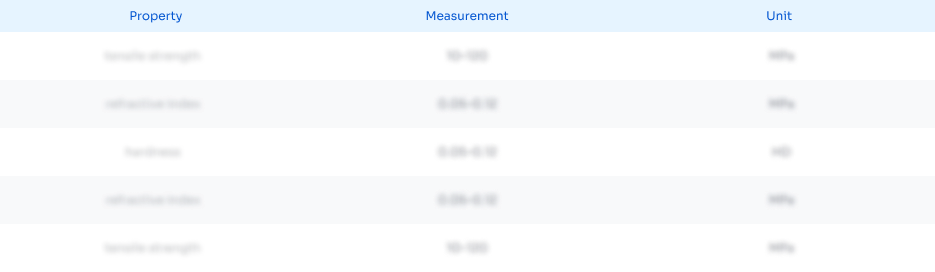
Abstract
Description
Claims
Application Information

- R&D
- Intellectual Property
- Life Sciences
- Materials
- Tech Scout
- Unparalleled Data Quality
- Higher Quality Content
- 60% Fewer Hallucinations
Browse by: Latest US Patents, China's latest patents, Technical Efficacy Thesaurus, Application Domain, Technology Topic, Popular Technical Reports.
© 2025 PatSnap. All rights reserved.Legal|Privacy policy|Modern Slavery Act Transparency Statement|Sitemap|About US| Contact US: help@patsnap.com