Preparation method of linear polydimethylsilane (PDMS) modified oil-water separation film, and oil-water separation film prepared through preparation method
A polydimethylsilane and oil-water separation membrane technology, which is applied in the field of oil-water separation material preparation, can solve the problems of low antifouling performance and high viscosity oil-water separation flux, etc., so as to improve antifouling performance, reduce pollution, and improve separation The effect of flux
- Summary
- Abstract
- Description
- Claims
- Application Information
AI Technical Summary
Problems solved by technology
Method used
Image
Examples
Embodiment 1
[0045] A preparation method of a linear polydimethylsilane modified oil-water separation membrane, comprising the steps of:
[0046] S1. Cleaning of the stainless steel mesh base: put the stainless steel mesh base into acetone, isopropanol and deionized water solvents in sequence, and ultrasonically clean them for 30 minutes to remove organic impurities on the surface, and then place them in a vacuum drying oven at 60°C for drying ;
[0047] S2. Surface plasma treatment: Put the clean stainless steel mesh into the plasma treatment machine, set the intensity to 50W, and set the time to 20min to fully hydroxylate the surface;
[0048] S3. Grafting of the flexible polymer brush liquid layer on the surface of the membrane: immerse the hydroxylated stainless steel mesh into the methyl-terminated PDMS liquid with a molecular weight of 6000 (Mw), place it in a blast drying oven, and set the temperature The temperature is 100℃, and the time is set to 24h;
[0049] S4. Take the stain...
Embodiment 2
[0056] A preparation method of a linear polydimethylsilane modified oil-water separation membrane, comprising the steps of:
[0057] S1. Cleaning of the stainless steel mesh substrate: put the stainless steel mesh substrate into acetone, isopropanol and deionized water solvents in sequence, and ultrasonically clean them for 30 minutes respectively to remove organic impurities on the surface, and place them in a vacuum drying oven at 60°C for drying;
[0058] S2. Surface plasma treatment: Put the clean stainless steel mesh into the plasma treatment machine, set the intensity to 50W, and set the time to 15min to fully hydroxylate the surface;
[0059] S3. Grafting of the flexible polymer brush liquid layer on the surface of the membrane: immerse the hydroxylated stainless steel mesh into the methyl-terminated PDMS liquid with a molecular weight of 9000 (Mw), place it in a blast drying oven, and set the temperature The temperature is 100°C, and the time is set to 24h. The linear...
Embodiment 3
[0062] A preparation method of a linear polydimethylsilane modified oil-water separation membrane, comprising the steps of:
[0063] S1. Cleaning of the stainless steel mesh substrate: put the stainless steel mesh substrate into acetone, isopropanol and deionized water solvents in sequence, and ultrasonically clean them for 30 minutes respectively to remove organic impurities on the surface, and place them in a vacuum drying oven at 60°C for drying;
[0064] S2. Surface plasma treatment: Put the clean stainless steel mesh into the plasma treatment machine, set the intensity to 30W, and set the time to 20min to fully hydroxylate the surface;
[0065] S3. Grafting of the flexible polymer brush liquid layer on the surface of the membrane: immerse the hydroxylated stainless steel mesh into the hydroxyl-terminated PDMS liquid with a molecular weight of 6000 (Mw), place it in a blast drying oven, and set the temperature to 100°C, the time is set to 24h. The linear PDMS molecular fo...
PUM
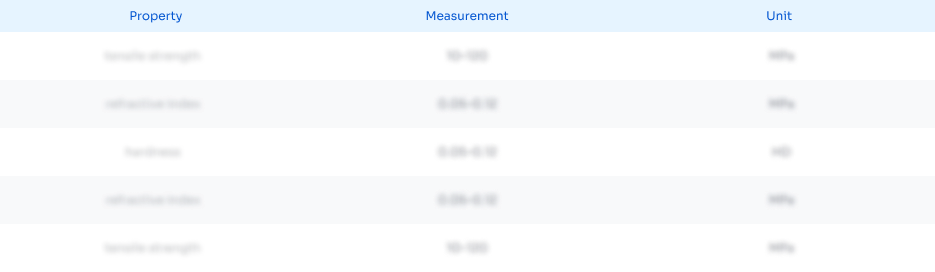
Abstract
Description
Claims
Application Information

- R&D
- Intellectual Property
- Life Sciences
- Materials
- Tech Scout
- Unparalleled Data Quality
- Higher Quality Content
- 60% Fewer Hallucinations
Browse by: Latest US Patents, China's latest patents, Technical Efficacy Thesaurus, Application Domain, Technology Topic, Popular Technical Reports.
© 2025 PatSnap. All rights reserved.Legal|Privacy policy|Modern Slavery Act Transparency Statement|Sitemap|About US| Contact US: help@patsnap.com