PI parameter setting method for asynchronous motor speed-sensorless speed adjustment system
A technology without speed sensor and speed regulation system, applied in control systems, control generators, vector control systems, etc., can solve problems such as difficulty in obtaining, and achieve the effects of high accuracy, strong adaptability, and improved practicability
- Summary
- Abstract
- Description
- Claims
- Application Information
AI Technical Summary
Problems solved by technology
Method used
Image
Examples
Embodiment Construction
[0041] The technical solutions in the embodiments of the present invention will be clearly and completely described and discussed below in conjunction with the accompanying drawings. Apparently, what is described here are only some examples of the present invention.
[0042] figure 1 In the transfer function model of the speed loop of the speed sensorless speed control system shown, ω r is the given angular frequency, ω m is the actual angular frequency, ω f is the feedback angular frequency, K t is the torque coefficient, T ω is the speed feedback delay time, and J is the moment of inertia of the transmission shaft converted to the motor side. In order to get accurate speed loop PI parameters, it is necessary to study and estimate T ω method and verify its feasibility.
[0043] figure 2 is the transfer function model of the actual speed value and the estimated value of the speed sensorless speed control system, where, Estimation of flux linkage for the ro...
PUM
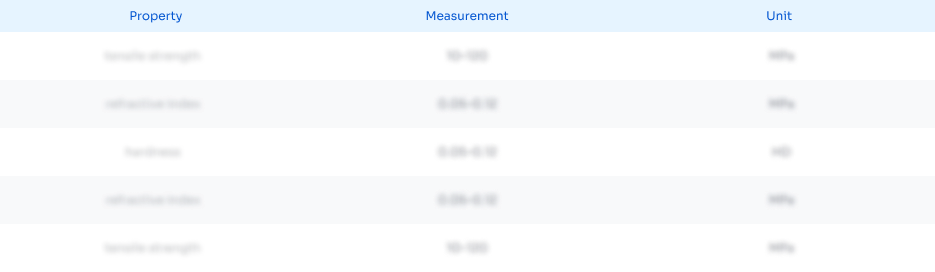
Abstract
Description
Claims
Application Information

- Generate Ideas
- Intellectual Property
- Life Sciences
- Materials
- Tech Scout
- Unparalleled Data Quality
- Higher Quality Content
- 60% Fewer Hallucinations
Browse by: Latest US Patents, China's latest patents, Technical Efficacy Thesaurus, Application Domain, Technology Topic, Popular Technical Reports.
© 2025 PatSnap. All rights reserved.Legal|Privacy policy|Modern Slavery Act Transparency Statement|Sitemap|About US| Contact US: help@patsnap.com