Method for lowering chromium pollution risk in electric furnace slag
A technology for electric furnace steel slag and chromium pollution, applied in the field of metallurgy, can solve problems such as low cooling rate and pollution, and achieve the effects of low energy consumption, treatment cost advantages, and thorough detoxification
- Summary
- Abstract
- Description
- Claims
- Application Information
AI Technical Summary
Problems solved by technology
Method used
Examples
Embodiment 1
[0025] After the stainless steel slag produced by the electric furnace is normally discharged, put the molten stainless steel slag into the slag tank. The main components of the stainless steel slag are CaO 46.8%, SiO 2 31.2%, MgO 10%, Al 2 o 3 4%, FeO 3%, Cr 2 o 3 5%.
[0026] Will Al 2 o 3 The modifier is added to the molten stainless steel slag, and the stainless steel slag and Al 2 o 3 Additives are mixed evenly to form molten mixed slag, in which Al 2 o 3 The mass of the additive is 8% of the molten stainless steel slag. Al 2 o 3 Grinding to a particle size of ≤74 mesh.
[0027] Lower the molten stainless steel slag at 3°C / min to below 1300°C to obtain a slag in which chromium mainly occurs in the spinel phase; The leaching concentration is lower than 0.01mg / L.
Embodiment 2
[0029] After the stainless steel slag produced by the electric furnace is normally discharged, put the molten stainless steel slag into the slag pot. The main components of the stainless steel slag are CaO 48%, SiO 2 32%, MgO 8%, Al 2 o 3 4%, FeO 3%, Cr 2 o 3 5%.
[0030] FeC 2 o 4 2H 2 O is added to the molten stainless steel slag, and the stainless steel slag and FeC are mixed by stirring 2 o 4 2H 2 O additives are mixed evenly to form molten mixed slag, wherein the added amount of FeO after conversion is 6% of the molten stainless steel slag. FeC 2 o 4 2H 2 The O additive is ground to a particle size of ≤74 mesh.
[0031] Lower the molten stainless steel slag at 3°C / min to below 1300°C to obtain a slag in which chromium mainly occurs in the spinel phase; The leaching concentration is lower than 0.10mg / L.
Embodiment 3
[0033] After the stainless steel slag produced by the electric furnace is normally discharged, put the molten stainless steel slag into the slag pot. The main components of the stainless steel slag are CaO 48%, SiO 2 32%, MgO 8%, Al 2 o 3 4%, FeO 3%, Cr 2 o 3 5%.
[0034] The MnO powder is added to the molten stainless steel slag, and the stainless steel slag and the MnO additive are mixed evenly by stirring to form a molten mixed slag, wherein the added amount of MnO is 8% of the molten stainless steel slag. MnO is ground to a particle size of ≤74 mesh.
[0035] Lower the molten stainless steel slag at 3°C / min to below 1300°C to obtain a slag in which chromium mainly occurs in the spinel phase; The leaching concentration is lower than 0.12mg / L.
PUM
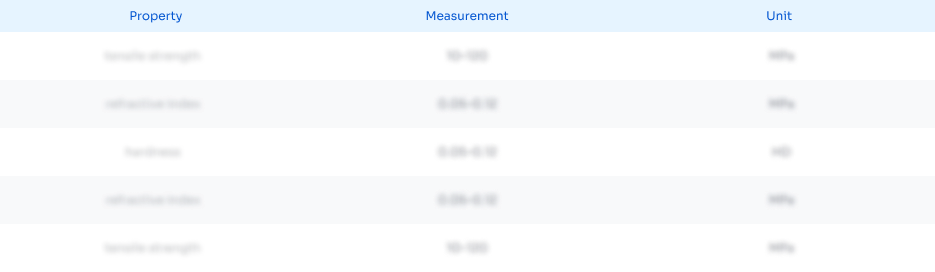
Abstract
Description
Claims
Application Information

- Generate Ideas
- Intellectual Property
- Life Sciences
- Materials
- Tech Scout
- Unparalleled Data Quality
- Higher Quality Content
- 60% Fewer Hallucinations
Browse by: Latest US Patents, China's latest patents, Technical Efficacy Thesaurus, Application Domain, Technology Topic, Popular Technical Reports.
© 2025 PatSnap. All rights reserved.Legal|Privacy policy|Modern Slavery Act Transparency Statement|Sitemap|About US| Contact US: help@patsnap.com