A method for detoxification of chromium-containing waste residue and recovery of chromium
A chromium waste slag and chromium recovery technology, applied in the direction of improving process efficiency, etc., can solve problems such as inability to efficiently recover chromium resources, chromium slag environmental hazards, consumption of acid and alkali, etc., to achieve full slag utilization, high social benefits and Economic benefit and low cost effect
- Summary
- Abstract
- Description
- Claims
- Application Information
AI Technical Summary
Problems solved by technology
Method used
Examples
Embodiment 1
[0023] (1) Take 0.5 tons of chromium-containing electroplating sludge (the main phases are calcium hydroxide and calcium carbonate), carry out aerobic roasting at 400° C. in ambient air, and grind after natural cooling.
[0024] (2) Ultrasonic the chromium-containing electroplating sludge treated in step (1) for 30 min at a frequency of 10 kHz.
[0025] (3) Put the chromium-containing electroplating sludge treated in step (2) into a hydrothermal kettle, then add water to make the solid-to-liquid ratio (w / w) 1:0.5, fully stir, add hydrochloric acid, sodium bicarbonate, Sodium carbonate, so that the concentration of hydrochloric acid in the system is 2mol / L, the concentration of sodium bicarbonate is 1mol / L, and the concentration of sodium carbonate is 1mol / L, fully stir, close the hydrothermal kettle, set the temperature to 60°C, and keep warm for reaction After 8 hours, cool naturally and slowly to room temperature, let stand for 12 hours, pour out the supernatant containing h...
Embodiment 2
[0029] (1) Take 1 ton of chromium-containing waste residue (main phases are hydrotalcite, hydrocalumite, calcium hydroxide, and magnesium oxide), perform aerobic roasting at 500° C. in ambient air, and grind after natural cooling.
[0030] (2) Ultrasonic the chromium-containing electroplating sludge treated in step (1) for 10 min at a frequency of 12 kHz.
[0031] (3) Put the chromium-containing electroplating sludge treated in step (2) into a hydrothermal kettle, then add water to make the solid-to-liquid ratio (w / w) 1:3, fully stir, add hydrochloric acid, sodium bicarbonate, Sodium carbonate, make the concentration of hydrochloric acid in the system be 2mol / L, the concentration of sodium bicarbonate is 1.5mol / L, the concentration of sodium carbonate is 0.3mol / L, fully stir, close hydrothermal kettle, setting temperature is 100 ℃, After heat preservation reaction for 4 hours, naturally and slowly cool to room temperature, let stand for 0.5 hours, pour out the supernatant cont...
Embodiment 3
[0034] (1) Take 2 tons of chromium-containing waste slag (the main phases are calcium hydroxide, magnesium hydroxide, ettringite, magnesium oxide, silicon dioxide), and carry out aerobic roasting at 800 ° C in ambient air, and carry out after natural cooling grind.
[0035] (2) Ultrasonic the chromium-containing electroplating sludge treated in step (1) for 50 min at a frequency of 15 kHz.
[0036] (3) Put the chromium-containing electroplating sludge treated in step (2) into a hydrothermal kettle, then add water to make the solid-to-liquid ratio (w / w) 1:5, stir well, add hydrochloric acid, sodium bicarbonate, Sodium carbonate, so that the concentration of hydrochloric acid in the system is 0.5mol / L, the concentration of sodium bicarbonate is 1mol / L, the concentration of sodium carbonate is 0.5mol / L, fully stir, close the hydrothermal kettle, set the temperature to 40 ℃, After heat preservation reaction for 12 hours, cool naturally and slowly to room temperature, let it stand...
PUM
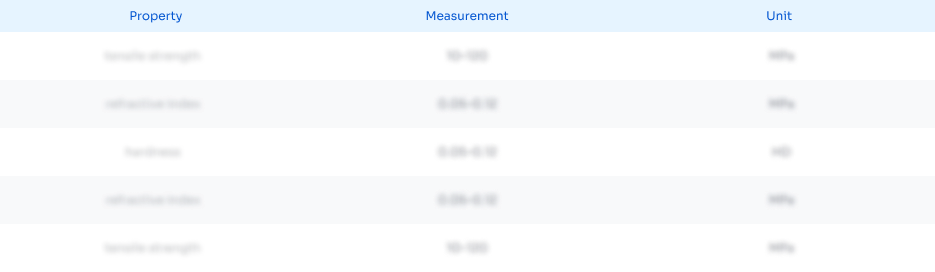
Abstract
Description
Claims
Application Information

- Generate Ideas
- Intellectual Property
- Life Sciences
- Materials
- Tech Scout
- Unparalleled Data Quality
- Higher Quality Content
- 60% Fewer Hallucinations
Browse by: Latest US Patents, China's latest patents, Technical Efficacy Thesaurus, Application Domain, Technology Topic, Popular Technical Reports.
© 2025 PatSnap. All rights reserved.Legal|Privacy policy|Modern Slavery Act Transparency Statement|Sitemap|About US| Contact US: help@patsnap.com