Method for quick additive manufacturing of large-scale bimetal spare parts
A technology for additive manufacturing and metal parts, which is applied in the field of rapid additive manufacturing of large parts and the preparation of new metal parts, which can solve the problems of unsuitable printing accuracy and slow printing speed.
- Summary
- Abstract
- Description
- Claims
- Application Information
AI Technical Summary
Problems solved by technology
Method used
Image
Examples
preparation example Construction
[0032] The process of the preparation method of the present invention is as follows:
[0033] S1. In a sealed chamber, use the Selective Laser Melting (SLM) process to print the bottom and side walls of the bottom contour of the metal part on a stainless steel metal substrate, and the bottom and sides of the printed contour The wall thickness is controlled between 0.5mm-5mm, and the height of the printed outer contour is controlled between 5-20mm.
[0034] S2. After the printing is completed, use the powder suction device 9 in the working chamber 1 to suck away the metal powder within the outer contour of the bottom.
[0035] S3. Use a plasma arc additive process to fill the inner space of the outer contour 4 with a metal material 10, and the top surface of the filled metal material 10 is slightly lower than the top surface of the outer contour. Among them, the height of the filled metal material 10 is controlled between 1.5-9mm, and the height difference between the metal material ...
PUM
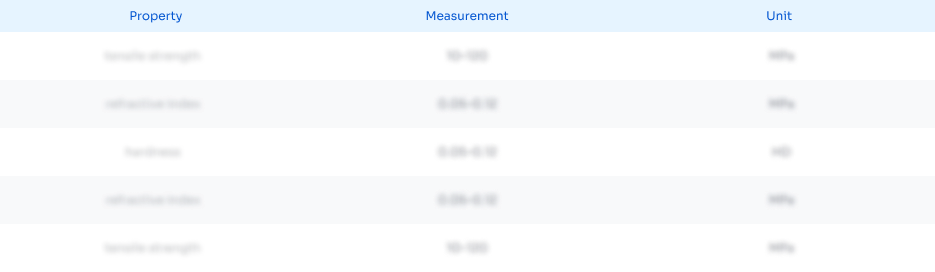
Abstract
Description
Claims
Application Information

- R&D Engineer
- R&D Manager
- IP Professional
- Industry Leading Data Capabilities
- Powerful AI technology
- Patent DNA Extraction
Browse by: Latest US Patents, China's latest patents, Technical Efficacy Thesaurus, Application Domain, Technology Topic, Popular Technical Reports.
© 2024 PatSnap. All rights reserved.Legal|Privacy policy|Modern Slavery Act Transparency Statement|Sitemap|About US| Contact US: help@patsnap.com