Control method and controller for 3D (three-dimension) printing and scanning
A technology of 3D printing and control method, applied in the field of control and control device for 3D printing scanning, can solve the problem of high precision, mechanical stress, fatigue strength, high deformation quantity, poor molding accuracy of parts, and poor surface finish and other problems, to achieve the effect of improving surface finish, improving contour accuracy, facilitating area division and printing and scanning
- Summary
- Abstract
- Description
- Claims
- Application Information
AI Technical Summary
Problems solved by technology
Method used
Image
Examples
Embodiment Construction
[0029] A further detailed description will be made below in conjunction with the accompanying drawings and embodiments of the present invention:
[0030] Such as figure 1 As shown, a control method for 3D printing scanning is characterized in that it includes the following steps:
[0031] A. Comparing the area overlap of the upper and lower adjacent printing and scanning layers, the overlapping printing and scanning area in the two layers is divided into a stacking area, and the non-overlapping printing and scanning area is divided into a layer difference area. Among them, in the same printing and scanning layer, first Print and scan the layered area, and then print and scan the layered area, and relatively reduce the printing and scanning power in the layered area, and relatively increase the printing and scanning power in the layered area;
[0032] B. Detect the outline of the stacked area, and divide the stacked area into two areas: the outline area and the filled area. Wh...
PUM
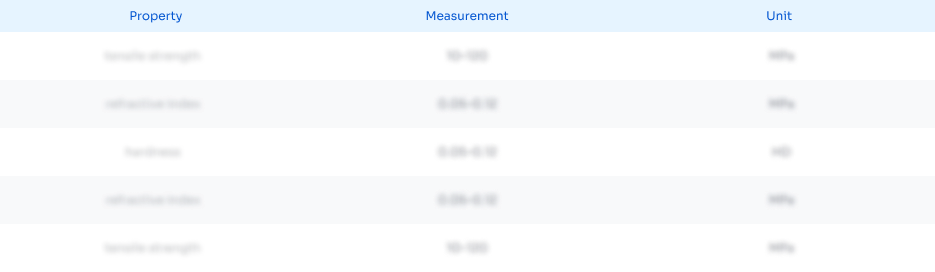
Abstract
Description
Claims
Application Information

- R&D
- Intellectual Property
- Life Sciences
- Materials
- Tech Scout
- Unparalleled Data Quality
- Higher Quality Content
- 60% Fewer Hallucinations
Browse by: Latest US Patents, China's latest patents, Technical Efficacy Thesaurus, Application Domain, Technology Topic, Popular Technical Reports.
© 2025 PatSnap. All rights reserved.Legal|Privacy policy|Modern Slavery Act Transparency Statement|Sitemap|About US| Contact US: help@patsnap.com