Full-cereal powder production technology
A technology of whole grain flour and production process, applied in the field of food processing, can solve the problems of loss of nutrients such as protein, low dough stability time, loss of natural flavor, etc., and achieve good taste, low starch damage, and maintain nutrition and flavor. Effect
- Summary
- Abstract
- Description
- Claims
- Application Information
AI Technical Summary
Problems solved by technology
Method used
Image
Examples
Embodiment 1
[0167] Embodiment 1: Discontinuous production
[0168] The vibratory grinding unit adopts discontinuous vibratory grinding, and the filling rate of the grinding body is 30-95% (volume filling rate), preferably 40-80%, and optimally 50-70%.
[0169] The material filling rate is 3-20% (volume filling rate), the optimal one is 5-16%, and the optimal one is 10-13%.
[0170] Segmented grinding, the grinding time of each stage can be selected from: 1 minute to 30 minutes, 1 minute to 20 minutes, 1 minute to 3 minutes, 3 minutes to 6 minutes, 13 seconds to 360 seconds, 13 seconds to 90 seconds, 31 seconds seconds to 130 seconds, 31 seconds to 60 seconds.
[0171] The grinding body is a rod, the vibration frequency is 16-18Hz, and the vibration acceleration is 3-6G;
[0172] After the raw material is ground once, it is sieved, and the sieve mesh can be selected from 40 mesh to 130 mesh. The material on the sieve returns to the same vibration grinding unit to continue grinding, and ...
Embodiment 2
[0173] Embodiment two: circular production
[0174] The vibrating grinding unit adopts continuous vibrating grinding, and the filling rate of the grinding body is 30-95% (volume filling rate), and the optimal one is 40-80%, and the optimal one is 50-70%. The grinding body is a rod, and the length-to-diameter ratio is 8:1-1:1, the optimized one is 6:1-2:1, the optimized one is 6:1-3:1, and the optimized one is 6:1-4:1. The vibration frequency of the grinding body is 12-13 Hz, and the amplitude is 6 mm.
[0175] Through the combination of continuous vibration grinding and screening, the circular production is realized. Screening equipment can choose vibrating screen, shaking screen, drum screen and so on.
[0176] Raw materials are vibratingly ground and sieved in the vibrating grinding unit, and the sieve mesh can be selected from 60 mesh to 110 mesh. The material on the sieve returns to the vibrating mill of the same vibrating grinding unit to continue grinding, and the mat...
Embodiment 3
[0179] Embodiment three: continuous production
[0180] The vibrating grinding unit adopts continuous vibrating grinding, and the filling rate of the grinding body is 30-95% (volume filling rate), and the optimal one is 40-80%, and the optimal one is 50-70%. The grinding body is a rod, the aspect ratio is 8:1~1:1, the optimized one is 6:1~2:1, the optimized one is 6:1~3:1, the optimized one is 6:1~4:1, The vibration frequency is 15-19Hz, and the amplitude is 6mm.
[0181] Through the combination of continuous vibration grinding and screening, continuous production is realized. Screening equipment can choose vibrating screen, shaking screen, drum screen and so on.
[0182] The cleaned wheat enters the vibrating mill and is ground in the shortest possible time. After being discharged, it is sieved with 76 meshes. Mesh sieving, the under-sieve enters the finished product mixing chamber, the over-sieve enters the third vibrating grinding unit for grinding, and then passes throu...
PUM
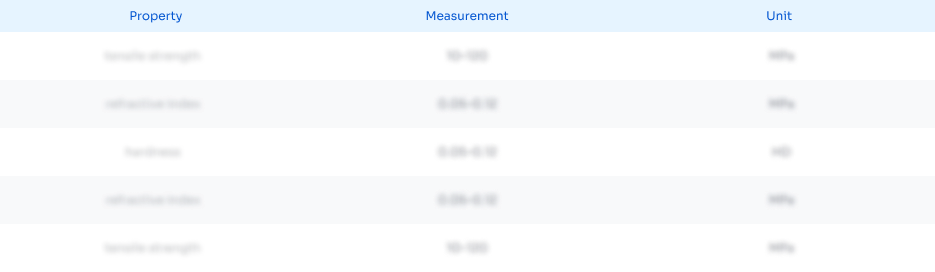
Abstract
Description
Claims
Application Information

- R&D
- Intellectual Property
- Life Sciences
- Materials
- Tech Scout
- Unparalleled Data Quality
- Higher Quality Content
- 60% Fewer Hallucinations
Browse by: Latest US Patents, China's latest patents, Technical Efficacy Thesaurus, Application Domain, Technology Topic, Popular Technical Reports.
© 2025 PatSnap. All rights reserved.Legal|Privacy policy|Modern Slavery Act Transparency Statement|Sitemap|About US| Contact US: help@patsnap.com