Novel composite insulator and production process thereof
A composite insulator, a new type of technology, applied in the production process of composite insulators and the field of new composite insulators, can solve the problems of easy to be broken by strong wind, weak interface bonding, poor product insulation, etc., to reduce the risk of use and operation. , The bonding is firm, and the effect of reducing the point of the interface
- Summary
- Abstract
- Description
- Claims
- Application Information
AI Technical Summary
Problems solved by technology
Method used
Image
Examples
Embodiment Construction
[0013] The present invention is further described in conjunction with the following examples.
[0014] A specific embodiment of a novel composite insulator of the present invention, such as figure 1 As shown, it includes a mandrel 1, a silicone rubber sheath 2 and an umbrella skirt 3, the silicone rubber sheath 2 is fixedly sleeved on the outer surface of the mandrel 1 by extrusion, and the silicone rubber sheath 2 includes a sheath The body, the outer surface of the sheath body has four protruding lines 21 extending in a cross shape, and the shed 3 is molded on the outer surface of the silicone rubber sheath 2 by injection.
[0015] In the new composite insulator of this embodiment, compared with the prior art, the silicone rubber sheath 2 is fixed on the outer surface of the mandrel 1 by extrusion, and the shed 3 is fixed on the outer surface of the silicone rubber sheath 2 by injection. The outer surface, so that the bonding between the silicone rubber sheath 2 and the man...
PUM
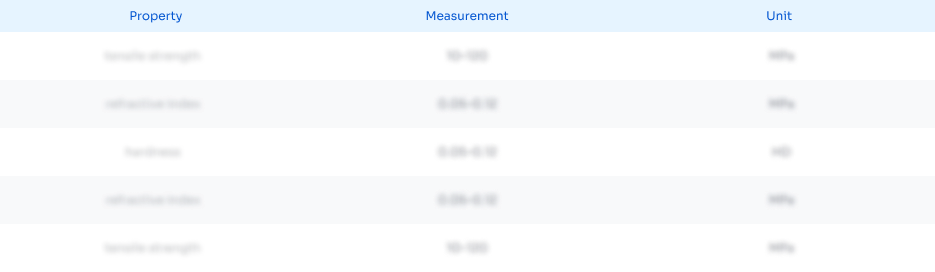
Abstract
Description
Claims
Application Information

- R&D
- Intellectual Property
- Life Sciences
- Materials
- Tech Scout
- Unparalleled Data Quality
- Higher Quality Content
- 60% Fewer Hallucinations
Browse by: Latest US Patents, China's latest patents, Technical Efficacy Thesaurus, Application Domain, Technology Topic, Popular Technical Reports.
© 2025 PatSnap. All rights reserved.Legal|Privacy policy|Modern Slavery Act Transparency Statement|Sitemap|About US| Contact US: help@patsnap.com