Method for separating iron element, magnesium element and aluminium element from calcium-removed calcium carbide slag
A technology for separating calcium carbide slag and iron, which is applied in the field of separating iron from calcium carbide slag for magnesium and aluminum elements, can solve the problem of low recycling rate of calcium carbide slag, and achieve the effects of low processing cost, low consumption, and small environmental emissions
- Summary
- Abstract
- Description
- Claims
- Application Information
AI Technical Summary
Problems solved by technology
Method used
Image
Examples
Embodiment 1
[0044] Get calcium carbide filter residue 500 grams after decalcification treatment, put into 1000ml beaker, add mass fraction and be 40% dilute sulfuric acid after filter residue is dissolved, filter insoluble residue, filtrate is vitriol solution (for extracting the raw material of metal ion ), add acid to adjust PH<2.5; the sulfate solution is gradually added dropwise to 3000g extraction solution I (extractant in the extraction solution I is triethylamine, trioctylamine and C18 alkane with a molar ratio of 1:6:3) The mixed solution of dimethylamine, the solvent is kerosene or sulfonated kerosene, and the mass percent of the extractant is 30%) in a 5000ml reactor, stirring continuously for 3-5 hours, then transferred to the oil-water separator, and the upper layer oil The phases were separated and collected to obtain 3033.6 g of an iron-containing organic solution, and the lower aqueous phase was a sulfate solution containing magnesium and aluminum;
[0045] Drop the iron-co...
Embodiment 2
[0049]Get calcium carbide filter residue 500 grams after decalcification treatment, put into 1000ml beaker, add mass fraction and be 40% dilute sulfuric acid after filter residue is dissolved, filter insoluble residue, filtrate is vitriol solution (for extracting the raw material of metal ion ), adding acid to adjust PH<2.5; the sulfate solution is gradually added dropwise to 3000g extraction solution I (in the extraction solution I, the extraction agent is dioctylamine, and the solvent is 150# aromatics, and the mass percentage of the extraction agent is 50%) In a 5000ml reactor, continue to stir for 3-5 hours, then transfer to the oil-water separator, separate and collect the upper oil phase to obtain 3033.6g of iron-containing organic solution; the lower water phase is a sulfate solution containing magnesium and aluminum;
[0050] Drop the iron-containing organic solution into 500 g of dilute sulfuric acid aqueous solution with a concentration of 50%, continue to stir for 2-...
Embodiment 3
[0054] Get calcium carbide filter residue 500 grams after decalcification treatment, put into 1000ml beaker, add mass fraction and be after the dilute hydrochloric acid of 40% filter residue is dissolved, a small amount of residue is filtered out, and filtrate is chloride salt solution (for extracting metal ion raw material), add acid to adjust PH<2.5; the chloride salt solution is gradually added dropwise to 3000g extraction solution I (extractant in the extraction solution I is triethylamine, trioctylamine and triethylamine with a molar ratio of 1:6:3 The mixed solution of C18 alkyldimethylamine, the solvent is aromatic hydrocarbon or alkylbenzene or the mixed solution of the two, the mass percentage of extractant is 70%) in the 5000ml reactor, keep stirring for 3-5 hours, then transfer to In the oil-water separator, the upper oil phase was separated and collected to obtain 3033.6 g of an iron-containing organic solution, and the lower aqueous phase was a sulfate solution con...
PUM
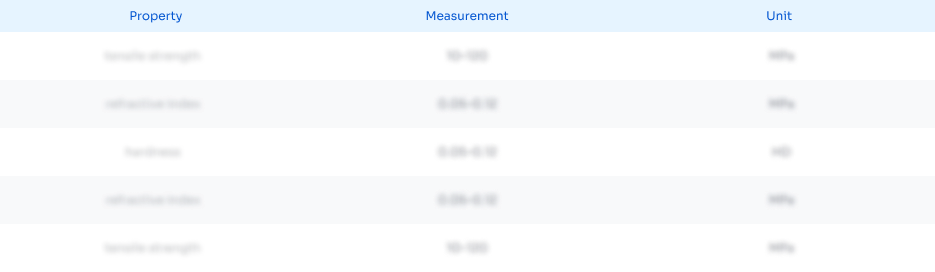
Abstract
Description
Claims
Application Information

- R&D Engineer
- R&D Manager
- IP Professional
- Industry Leading Data Capabilities
- Powerful AI technology
- Patent DNA Extraction
Browse by: Latest US Patents, China's latest patents, Technical Efficacy Thesaurus, Application Domain, Technology Topic, Popular Technical Reports.
© 2024 PatSnap. All rights reserved.Legal|Privacy policy|Modern Slavery Act Transparency Statement|Sitemap|About US| Contact US: help@patsnap.com