Mold temperature control method and system of injection molding machine
A mold temperature control and injection molding machine technology, applied in the field of mold temperature control methods and systems for injection molding machines, can solve problems such as difficulty in molding transparent optical products, reducing product surface quality, causing environmental pollution, etc. Fiber phenomenon, improve finish, solve the effect of surface shrinkage
- Summary
- Abstract
- Description
- Claims
- Application Information
AI Technical Summary
Problems solved by technology
Method used
Image
Examples
Embodiment Construction
[0024] The following are specific embodiments of the application and in conjunction with the accompanying drawings, further describe the technical solution of the application, but the application is not limited to these embodiments.
[0025] The mold temperature control method of an injection molding machine shown in the embodiment of this application can be applied to molding optical products with high transparency, plastic parts with microstructure on the surface, high-strength composite material parts, long thin-walled parts and other injection molded parts. During molding, various surface defects such as surface weld marks, flow marks, and depressions produced by traditional mold temperature control methods can be eliminated.
[0026] refer to figure 1 , figure 1 It is a flowchart of a mold temperature control method for an injection molding machine shown in an exemplary embodiment. The mold temperature control method for an injection molding machine is applied to an inje...
PUM
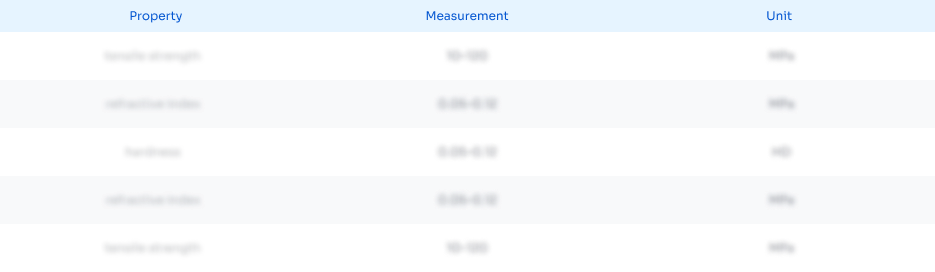
Abstract
Description
Claims
Application Information

- Generate Ideas
- Intellectual Property
- Life Sciences
- Materials
- Tech Scout
- Unparalleled Data Quality
- Higher Quality Content
- 60% Fewer Hallucinations
Browse by: Latest US Patents, China's latest patents, Technical Efficacy Thesaurus, Application Domain, Technology Topic, Popular Technical Reports.
© 2025 PatSnap. All rights reserved.Legal|Privacy policy|Modern Slavery Act Transparency Statement|Sitemap|About US| Contact US: help@patsnap.com