Improved variation mode decomposition diagnosis method for engine main shaft bearing fault diagnosis
A technology of variational mode decomposition and spindle bearings, which is applied in the testing of mechanical components, testing of machine/structural components, measuring devices, etc., can solve problems such as difficulty in breaking through the limitations of window functions, cross-interference, and hindering effective analysis of signals
- Summary
- Abstract
- Description
- Claims
- Application Information
AI Technical Summary
Problems solved by technology
Method used
Image
Examples
Embodiment example 2
[0098] Implementation case 2: Fault diagnosis of the outer ring of the engine main shaft bearing
[0099] According to the characteristic frequency formula of the bearing outer ring fault, the frequency of the bearing outer ring fault can be calculated:
[0100]
[0101] In formula (11), f s Indicates the sampling frequency, n indicates the number of rolling elements, d indicates the diameter of the rolling elements, D indicates the diameter of the pitch circle, and α indicates the contact angle of the bearing. The bearing model of this experiment is ER-12K, and the outer ring has early pitting corrosion failure. During the signal acquisition process, the sampling frequency is 25600Hz; the bearing is unloaded and the running speed is 2400r / min; the number of sampling points is 32768. The number of bearing rolling elements is 8, the rolling element diameter is 7.9375mm, and the pitch circle diameter is 33.4772mm. Select sample N=12288 as the original signal, and calculate...
PUM
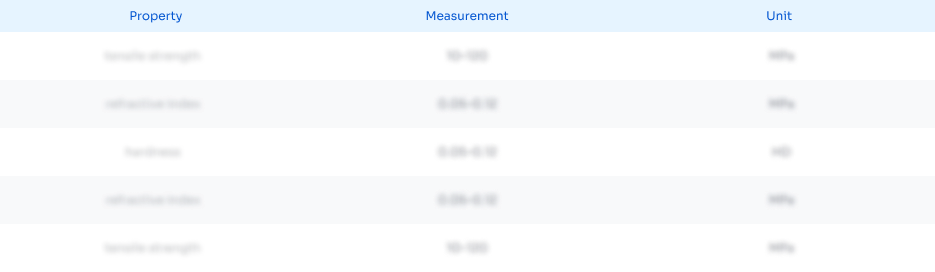
Abstract
Description
Claims
Application Information

- R&D
- Intellectual Property
- Life Sciences
- Materials
- Tech Scout
- Unparalleled Data Quality
- Higher Quality Content
- 60% Fewer Hallucinations
Browse by: Latest US Patents, China's latest patents, Technical Efficacy Thesaurus, Application Domain, Technology Topic, Popular Technical Reports.
© 2025 PatSnap. All rights reserved.Legal|Privacy policy|Modern Slavery Act Transparency Statement|Sitemap|About US| Contact US: help@patsnap.com