Vacuum cooling crystallization method
A vacuum cooling and crystallization technology, which is applied in crystallization separation, solution crystallization, separation methods, etc., can solve the problems of low energy efficiency, achieve significant economic benefits, avoid explosive nucleation, and reduce processing costs
- Summary
- Abstract
- Description
- Claims
- Application Information
AI Technical Summary
Problems solved by technology
Method used
Image
Examples
Embodiment 1
[0025] Add the mixed aqueous solution of sodium nitrate and potassium chloride at a temperature of 85°C to the crystallizer, and the feeding amount is 30m 3 , The crystallizer is a wenson batch vacuum crystallizer, and the body of the crystallizer container is lined with Q235-A rubber. The compressor adopts LC20000 type Roots compressor, and the motor power of the compressor is 280kW, and it is driven by frequency conversion. Turn on the vacuum pump and compressor, and the compressor sucks the steam in the crystallizer. When the temperature drops to 80°C, the potassium nitrate in the solution reaches saturation and begins to crystallize. The water in the crystallizer vaporizes and flashes, forming secondary The steam enters the compressor to be compressed, and the heated secondary steam enters the condenser to condense, and the condensate of the formed secondary steam is discharged into the condensate tank, and the non-condensable gas in the system is discharged from the syste...
Embodiment 2
[0027] Add the mixed aqueous solution of magnesium nitrate and potassium chloride at a temperature of 90°C to the crystallizer, and the feeding amount is 30m 3 , The crystallizer is a wenson batch vacuum crystallizer, and the body of the crystallizer container is lined with Q235-A rubber. The compressor adopts LC20000 type Roots compressor, and the motor power of the compressor is 280kW, and it is driven by frequency conversion. Turn on the vacuum pump and compressor, and the compressor sucks the steam in the crystallizer. When the temperature drops to 80°C, the potassium nitrate in the solution reaches saturation and begins to crystallize. The water in the crystallizer vaporizes and flashes, forming secondary The steam enters the compressor to be compressed, and the heated secondary steam enters the condenser to condense, and the condensate of the formed secondary steam is discharged into the condensate pipe, and the non-condensable gas in the system is discharged from the sy...
Embodiment 3
[0029] Add the mixed aqueous solution of ammonium nitrate and potassium chloride at a temperature of 105°C to the crystallizer, and the feeding amount is 30m 3 , The crystallizer is a forced external circulation vacuum crystallizer, and the body of the crystallizer container is lined with Q235-A rubber. The compressor adopts LC20000 type Roots compressor, and the motor power of the compressor is 280kW, and it is driven by frequency conversion. Turn on the vacuum pump and compressor, and the compressor sucks the steam in the crystallizer. When the temperature drops to 80°C, the potassium nitrate in the solution reaches saturation and begins to crystallize. The water in the crystallizer vaporizes and flashes, forming secondary The steam enters the compressor to be compressed, and the heated secondary steam enters the condenser to condense, and the condensate of the formed secondary steam is discharged into the condensate tank, and the non-condensable gas in the system is dischar...
PUM
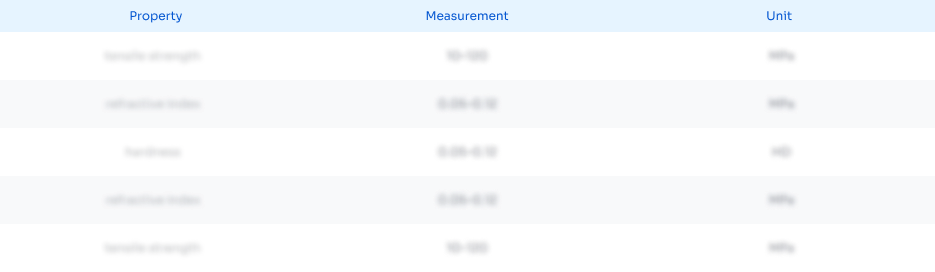
Abstract
Description
Claims
Application Information

- R&D
- Intellectual Property
- Life Sciences
- Materials
- Tech Scout
- Unparalleled Data Quality
- Higher Quality Content
- 60% Fewer Hallucinations
Browse by: Latest US Patents, China's latest patents, Technical Efficacy Thesaurus, Application Domain, Technology Topic, Popular Technical Reports.
© 2025 PatSnap. All rights reserved.Legal|Privacy policy|Modern Slavery Act Transparency Statement|Sitemap|About US| Contact US: help@patsnap.com