Core-shell type polymer microsphere and preparation method thereof
A polymer, core-shell technology, applied in the direction of drilling compositions, chemical instruments and methods, etc., can solve the problems of poor plugging effect, poor temperature resistance and salt resistance, instability, etc.
- Summary
- Abstract
- Description
- Claims
- Application Information
AI Technical Summary
Problems solved by technology
Method used
Image
Examples
Embodiment 1
[0039] The polymer microspheres of this embodiment are prepared by polymerizing a reverse-phase microemulsion under the action of a redox composite initiator; the reverse-phase microemulsion, in parts by weight, comprises the following components:
[0040] a) 50 parts of oil-soluble solvent; oil-soluble solvent is white oil;
[0041] b) 10 parts of emulsifier; the emulsifier HLB value is 6.7 (from Span 60 (ie sorbitan monostearate) HLB value 4.7; Tween 20 (polyoxyethylene (20EO) sorbitan monolauric acid Esters) mixed with HLB value 16.7);
[0042] c) 35 parts of hydrophilic monomers: 18 parts of acrylamide, 6 parts of sodium acrylate, 6 parts of 2-acrylamido-2-sodium methylpropanesulfonate and 5 parts of dimethyl diallyl ammonium chloride composition;
[0043] d) 5 parts of hydrophobic monomers: sodium 2-acrylamido-N-hexadecylsulfonate;
[0044] e) 30 parts of water;
[0045] Wherein, the composite initiator, in terms of the above-mentioned total monomer weight percent, co...
Embodiment 2
[0081] The polymer microspheres of this embodiment are prepared by polymerizing a reverse-phase microemulsion under the action of a redox composite initiator; the reverse-phase microemulsion, in parts by weight, comprises the following components:
[0082] a) 50 parts of oil-soluble solvent; oil-soluble solvent is white oil;
[0083] b) 10 parts of emulsifier; the emulsifier HLB value is 6.7 (from Span 60 (ie sorbitan monostearate) HLB value 4.7; Tween 20 (polyoxyethylene (20EO) sorbitan monolauric acid Esters) mixed with HLB value 16.7);
[0084] c) 35 parts of hydrophilic monomers: 18 parts of acrylamide, 6 parts of sodium acrylate, 6 parts of 2-acrylamido-2-sodium methylpropanesulfonate and 5 parts of dimethyl diallyl ammonium chloride composition;
[0085] d) 5 parts of hydrophobic monomers: octadecyl methacrylate;
[0086] e) 30 parts of water;
[0087] Wherein, the composite initiator, in terms of the above-mentioned total monomer weight percent, comprises the follow...
Embodiment 3
[0101] The polymer microspheres of this embodiment are prepared by polymerizing a reverse-phase microemulsion under the action of a redox composite initiator; the reverse-phase microemulsion, in parts by weight, comprises the following components:
[0102] a) 50 parts of oil-soluble solvent; oil-soluble solvent is white oil;
[0103] b) 10 parts of emulsifier; the emulsifier HLB value is 6.7 (from Span 60 (ie sorbitan monostearate) HLB value 4.7; Tween 20 (polyoxyethylene (20EO) sorbitan monolauric acid Esters) mixed with HLB value 16.7);
[0104] c) 35 parts of hydrophilic monomers: 18 parts of acrylamide, 6 parts of sodium acrylate, 6 parts of 2-acrylamido-2-sodium methylpropanesulfonate and 5 parts of dimethyl diallyl ammonium chloride composition;
[0105] d) 5 parts of hydrophobic monomers: p-tert-butylstyrene;
[0106] e) 30 parts of water;
[0107] Wherein, the composite initiator, in terms of the above-mentioned total monomer weight percent, comprises the following...
PUM
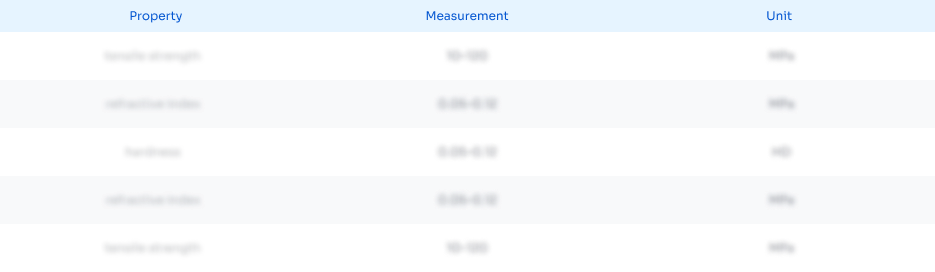
Abstract
Description
Claims
Application Information

- R&D
- Intellectual Property
- Life Sciences
- Materials
- Tech Scout
- Unparalleled Data Quality
- Higher Quality Content
- 60% Fewer Hallucinations
Browse by: Latest US Patents, China's latest patents, Technical Efficacy Thesaurus, Application Domain, Technology Topic, Popular Technical Reports.
© 2025 PatSnap. All rights reserved.Legal|Privacy policy|Modern Slavery Act Transparency Statement|Sitemap|About US| Contact US: help@patsnap.com