Rapid preparation method and application of high-yield MOF-derived catalyst
A catalyst and high-yield technology, applied in chemical instruments and methods, physical/chemical process catalysts, chemical/physical processes, etc., can solve problems such as harsh operating conditions, large energy loss, and cumbersome steps, and achieve increased reaction kinetics, Short time-consuming, process-safe results
- Summary
- Abstract
- Description
- Claims
- Application Information
AI Technical Summary
Problems solved by technology
Method used
Image
Examples
Embodiment 1
[0023] Take 20mL of deionized water, add 1.0g of dimethylimidazole, stir and dissolve to obtain solution A; take 40mL of deionized water, add 0.6g of cobalt chloride, stir and dissolve to obtain solution B; mix solution A and solution B, and After standing for 6 hours, the mixed solution and the precipitated product were suction-filtered and washed, and then dried at 50° C. to obtain Co-MOF powder. Co-MOF powders were mechanically compressed to obtain monolithic Co-MOF sheets. Subsequently, the obtained monolithic Co-MOF sheet was buried in graphene powder, and then the mixture was transferred to a microwave reactor, and nitrogen gas was introduced as a protective gas. The microwave radiation power was controlled at 800W, and the microwave radiation time was controlled at 90 seconds. The Co-MOF sheet derivatives were then removed from the mixture to obtain the Co-MOF-derived catalyst Co@NC. From XRD spectrum figure 1 It can be seen that Co exists in the form of simple metal ...
Embodiment 2
[0025] Take 10mL of deionized water, add 0.4g of dimethylimidazole, stir and dissolve to obtain solution A; take 20mL of deionized water, add 0.2g of cobalt chloride, stir and dissolve to obtain solution B; mix solution A and solution B, and After standing for 8 hours, the mixed solution and the precipitated product were suction-filtered and washed, and then dried at 80° C. to obtain Co-MOF powder. Co-MOF powders were mechanically compressed to obtain monolithic Co-MOF sheets. Subsequently, the obtained monolithic Co-MOF sheet was buried in graphene powder, and then the mixture was transferred to a microwave reactor, nitrogen gas was introduced as a protective gas, the microwave radiation power was controlled at 1000W, and the microwave radiation time was controlled at 30 seconds, and then The Co-MOF sheet derivatives were removed from the mixture to obtain the Co-MOF-derived catalyst Co@NC.
Embodiment 3
[0027] Take 50mL of deionized water, add 1.8g of dimethylimidazole, stir and dissolve to obtain solution A; take 30mL of deionized water, add 0.8g of cobalt chloride, stir and dissolve to obtain solution B; mix solution A and solution B, and then The carbon fiber paper was soaked in the mixed solution, and after standing for 8 hours, the carbon fiber paper was taken out, washed, and then dried at 50°C to obtain a carbon fiber paper supported Co-MOF precursor. Subsequently, the obtained carbon fiber paper-loaded Co-MOF precursor was buried in graphene powder, and then the mixture was transferred to a microwave reactor, and nitrogen gas was introduced as a protective gas. The microwave radiation power was controlled at 1000W, and the microwave radiation time was controlled at 30 seconds, and then remove the carbon fiber paper-supported Co-MOF precursor derivative from the mixture to obtain the catalyst carbon fiber paper-supported Co@NC / CF. from figure 2 It can be known from t...
PUM
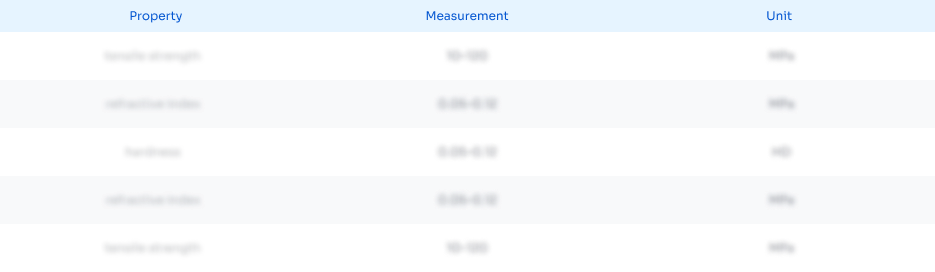
Abstract
Description
Claims
Application Information

- R&D Engineer
- R&D Manager
- IP Professional
- Industry Leading Data Capabilities
- Powerful AI technology
- Patent DNA Extraction
Browse by: Latest US Patents, China's latest patents, Technical Efficacy Thesaurus, Application Domain, Technology Topic, Popular Technical Reports.
© 2024 PatSnap. All rights reserved.Legal|Privacy policy|Modern Slavery Act Transparency Statement|Sitemap|About US| Contact US: help@patsnap.com