Cationic inverse emulsion thickener and preparation method thereof
An inverse emulsion and inverse emulsion polymerization technology, applied in the field of polymer materials, can solve problems such as unsatisfactory thickening ability, and achieve the effect of excellent thickening ability
- Summary
- Abstract
- Description
- Claims
- Application Information
AI Technical Summary
Problems solved by technology
Method used
Image
Examples
Embodiment 1
[0046] Add 277g of deionized water into the beaker, add 101g of acryloyloxyethyltrimethylammonium chloride and 124g of acrylamide under stirring, add 0.23g of N,N'-methylene bisacrylamide and 0.23 tert-butyl hydroperoxide, after continuing to stir and dissolve, adjust the pH value of the solution to 4-6 to form an aqueous phase solution.
[0047] Add 489g Marcol to another beaker TM 52. 411g Isopar TM C and 30g SPAN 80, stirred and dissolved evenly to obtain an oil phase solution.
[0048] In the state of stirring, slowly add the oil phase solution into the water phase solution, continue to stir for 2 minutes after the addition, and then use a homogenizer to homogenize for 2-5 minutes.
[0049] Transfer the homogenized emulsion to a four-necked flask equipped with a stirring paddle, a thermometer and a condenser, start stirring, and pass nitrogen gas for more than 30 minutes to remove oxygen in the system.
[0050] Dissolve 0.45 g of reducing agent sodium bisulfite in dei...
Embodiment 2
[0054] Add 337g of deionized water to the beaker, add 180g of acrylamidopropyltrimethylammonium chloride and 120g of hydroxyethyl acrylate under stirring, add 0.15g of diallylamine and 0.15g of potassium bromate after stirring and dissolving, and continue stirring After dissolving, adjust the pH value of the solution to 4-6 to form an aqueous phase solution.
[0055] Add 750g Isopar to another beaker TM M and 22.5g SPAN 60, stirred and dissolved evenly to obtain an oil phase solution.
[0056] In the state of stirring, slowly add the oil phase solution into the water phase solution, continue to stir for 2 minutes after the addition, and then use a homogenizer to homogenize for 2-5 minutes.
[0057] Transfer the homogenized emulsion to a four-necked flask equipped with a stirring paddle, a thermometer and a condenser, start stirring, and pass nitrogen gas for more than 30 minutes to remove oxygen in the system.
[0058] Dissolve 0.3 g of reducing agent sodium metabisulfite i...
Embodiment 3
[0062] Add 389g of deionized water to the beaker, add 281g of methacryloxyethyltrimethylammonium chloride and 94g of vinylpyrrolidone under stirring, add 0.038g of triallylamine and 0.075g of persulfuric acid after stirring and dissolving Ammonium, after continuing to stir and dissolve, adjust the pH value of the solution to 4-6 to form an aqueous phase solution.
[0063] Add 480g polyisobutylene, 120g Isopar to another beaker TM E and 52.5g Hypermer TM 2296, the oil phase solution was obtained after stirring and dissolving evenly.
[0064] In the state of stirring, slowly add the oil phase solution into the water phase solution, continue to stir for 2 minutes after the addition, and then use a homogenizer to homogenize for 2-5 minutes.
[0065] Transfer the homogenized emulsion to a four-necked flask equipped with a stirring paddle, a thermometer and a condenser, start stirring, and pass nitrogen gas for more than 30 minutes to remove oxygen in the system.
[0066] Disso...
PUM
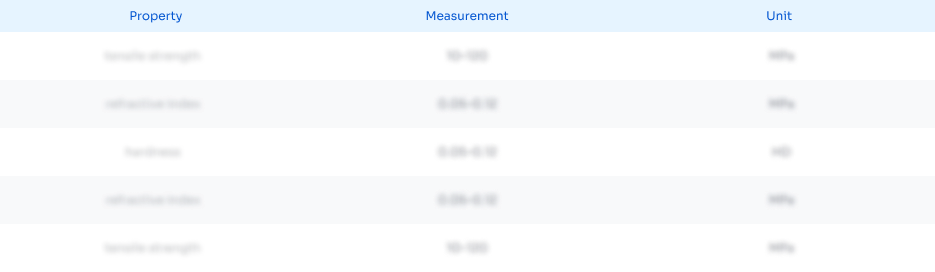
Abstract
Description
Claims
Application Information

- R&D Engineer
- R&D Manager
- IP Professional
- Industry Leading Data Capabilities
- Powerful AI technology
- Patent DNA Extraction
Browse by: Latest US Patents, China's latest patents, Technical Efficacy Thesaurus, Application Domain, Technology Topic, Popular Technical Reports.
© 2024 PatSnap. All rights reserved.Legal|Privacy policy|Modern Slavery Act Transparency Statement|Sitemap|About US| Contact US: help@patsnap.com