CCD full automatic high-precision needle grinding machine and needle grinding control method
A control method and a needle grinding technology, which are applied in the direction of automatic grinding control devices, grinding machine parts, and machine tools suitable for grinding the edge of workpieces, etc., which can solve problems such as poor precision, hidden dangers to employee safety, and high labor intensity , to achieve the effect of improving the accuracy
- Summary
- Abstract
- Description
- Claims
- Application Information
AI Technical Summary
Problems solved by technology
Method used
Image
Examples
Embodiment Construction
[0039] The present invention will be described in detail below in conjunction with the accompanying drawings and specific embodiments, where the schematic embodiments and descriptions of the present invention are used to explain the present invention, but not to limit the present invention.
[0040] refer to figure 1 The present invention also specifically discloses a needle grinding control method, which includes the following steps:
[0041] A needle grinding control method, comprising first inputting the coordinate parameters of the standard graphics of workpieces to be processed into the industrial computer 4, and then performing the following steps:
[0042] Step 1) Obtain the coordinates of the workpiece: clamp the first punching needle 309 of the spinneret to be processed on the clamping mechanism, start the CCD camera 312 through the industrial computer 4, and start the third rotation control motor 304, and obtain the coordinates of the workpiece through the rotation o...
PUM
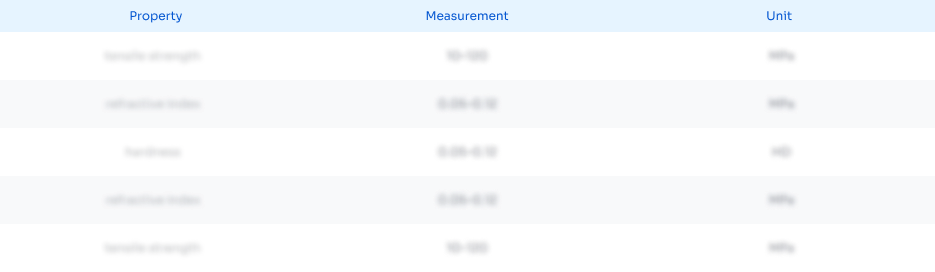
Abstract
Description
Claims
Application Information

- R&D
- Intellectual Property
- Life Sciences
- Materials
- Tech Scout
- Unparalleled Data Quality
- Higher Quality Content
- 60% Fewer Hallucinations
Browse by: Latest US Patents, China's latest patents, Technical Efficacy Thesaurus, Application Domain, Technology Topic, Popular Technical Reports.
© 2025 PatSnap. All rights reserved.Legal|Privacy policy|Modern Slavery Act Transparency Statement|Sitemap|About US| Contact US: help@patsnap.com