Method for temperature-control flotation and decalcification of magnesite
A technology of temperature control and magnesite, which is applied in flotation, solid separation, etc., can solve problems such as the influence of temperature and surface characteristics, and achieve the effects of saving mineral processing costs, stable operation, and low grade
- Summary
- Abstract
- Description
- Claims
- Application Information
AI Technical Summary
Problems solved by technology
Method used
Image
Examples
Embodiment 1
[0034] A method for temperature-controlled flotation decalcification of magnesite, the flow chart of which is shown in figure 1 , including the following steps:
[0035] Step 1: Grinding
[0036] Crushing and screening high-calcium and low-grade magnesite raw materials to obtain magnesite powder with a particle size of 38-74 μm;
[0037] Step 2: Blending
[0038] Put the magnesite powder with a particle size of 38-74 μm in the hanging tank type flotation machine, add deionized water and mix evenly, and adjust the slurry to obtain magnesite slurry; wherein, the content of magnesite in the magnesite slurry is The mass concentration is 10%;
[0039] Step 3: Positive Flotation Decalcification
[0040] Set the temperature of the magnesite slurry at 5°C, first add 3% NaOH aqueous solution to the magnesite slurry, adjust the pH value to 11, and stir for 2 minutes until the slurry is uniform to obtain magnesite with a pH value of 11 pulp;
[0041] To the magnesite slurry with a ...
Embodiment 2
[0044] A method for temperature-controlled flotation decalcification of magnesite, the same as in Example 1, the difference is that the temperature of the magnesite slurry is 10°C, and the main components of the obtained low-calcium magnesite concentrate are MgO is 47.23%, SiO 2 is 0.13% and CaO is 0.59%; the MgO in the low-calcium magnesite concentrate accounts for 68.15% of the total weight of MgO in the raw material.
Embodiment 3
[0046] A method for magnesite temperature-controlled flotation decalcification, the same as embodiment 1, the difference is that the temperature of the magnesite slurry is 15°C, and the main components of the obtained low-calcium magnesite concentrate are MgO is 48.23%, SiO 2 is 0.21%, CaO is 0.47%; MgO in the low-calcium magnesite concentrate accounts for 69.25% of the total weight of MgO in the raw material.
PUM
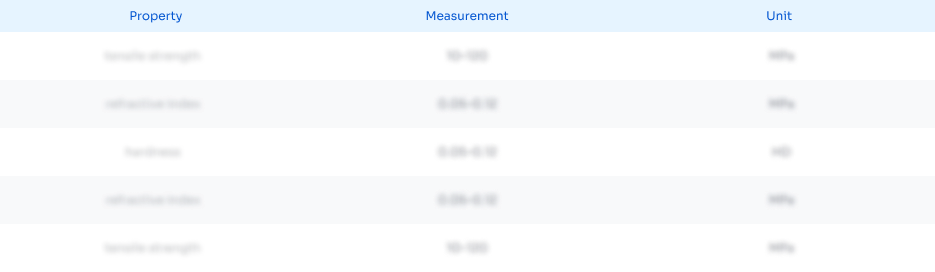
Abstract
Description
Claims
Application Information

- R&D
- Intellectual Property
- Life Sciences
- Materials
- Tech Scout
- Unparalleled Data Quality
- Higher Quality Content
- 60% Fewer Hallucinations
Browse by: Latest US Patents, China's latest patents, Technical Efficacy Thesaurus, Application Domain, Technology Topic, Popular Technical Reports.
© 2025 PatSnap. All rights reserved.Legal|Privacy policy|Modern Slavery Act Transparency Statement|Sitemap|About US| Contact US: help@patsnap.com