Aluminum alloy hot-rolled strip plate shape control method
A technology for shape control and hot-rolled strips, applied in metal rolling, metal rolling, profile control, etc., can solve the problems of no obvious help in shape control, expensive shape detectors, and high maintenance costs. Good shape, increase cost, meet the effect of shape requirements
- Summary
- Abstract
- Description
- Claims
- Application Information
AI Technical Summary
Problems solved by technology
Method used
Image
Examples
Embodiment
[0038] A 5052 aluminum alloy with a final rolling temperature of 320°C and a hot rolling state of F state, produced on a 1+3 hot rolling mill, with a strip temperature detector installed only before the entrance of the last stand F3. The roll diameter of the last stand F3 is 700mm, the production thickness is 2.5mm, the width is 1450mm, and the total length of the strip is 1000m. During the rolling process, the rolling preset roll gap is 2.43mm, and the production method of the plate shape control is as follows:
[0039] 1. Reasonably install the entrance strip high temperature detector, the temperature detection range is 100~500℃, and the measurement accuracy is -1~+1℃.
[0040] 2. Online detection of the transverse temperature of the incoming strip, real-time detection of the temperature during the rolling process, and detection of the temperature distribution in the width direction of the aluminum alloy strip.
[0041] 3. According to the feedback temperature characteristic c...
PUM
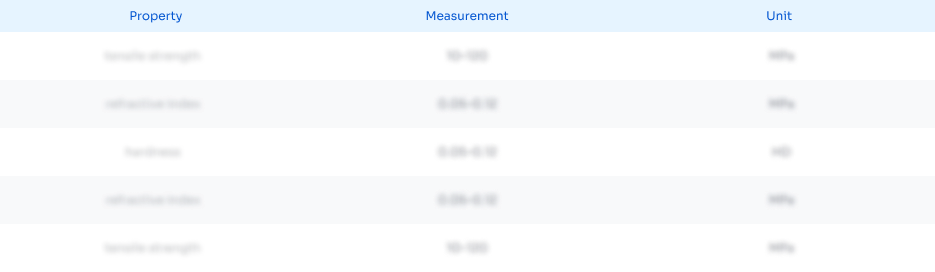
Abstract
Description
Claims
Application Information

- R&D
- Intellectual Property
- Life Sciences
- Materials
- Tech Scout
- Unparalleled Data Quality
- Higher Quality Content
- 60% Fewer Hallucinations
Browse by: Latest US Patents, China's latest patents, Technical Efficacy Thesaurus, Application Domain, Technology Topic, Popular Technical Reports.
© 2025 PatSnap. All rights reserved.Legal|Privacy policy|Modern Slavery Act Transparency Statement|Sitemap|About US| Contact US: help@patsnap.com