A method for peeling the surface of a traction motor rotor guide bar
A processing method and technology for rotor bars, which are used in the manufacture of motor generators, electromechanical devices, electrical components, etc., can solve the problems of poor surface quality consistency of finished products, poor product surface consistency, and high rework and maintenance intensity, so as to improve the surface quality. The effect of good quality, surface consistency and low scrap rate
- Summary
- Abstract
- Description
- Claims
- Application Information
AI Technical Summary
Problems solved by technology
Method used
Image
Examples
Embodiment Construction
[0038] A method for peeling the surface of a traction motor rotor guide bar, the process steps of the treatment method are:
[0039] S1: Drawing and matching mold
[0040] Calculate the total deformation required for drawing according to the product performance requirements, then calculate the number of passes required for drawing according to the total deformation, and then determine the size and specification of the mold socket interface according to the deformation between the drawing passes;
[0041] S2: Modeling
[0042] ①Processing mold core
[0043] The mold core material is YG8, and the material specifications of the mold core are calculated according to the cross-sectional size of the guide bar. Generally, a circular mold core is used, and the outer circle size of the mold core is 40mm larger than the maximum size of the finished product. During processing, the mold cutting edge is parallel to the guide bar. Around the plane, in order to facilitate peeling and chip ...
PUM
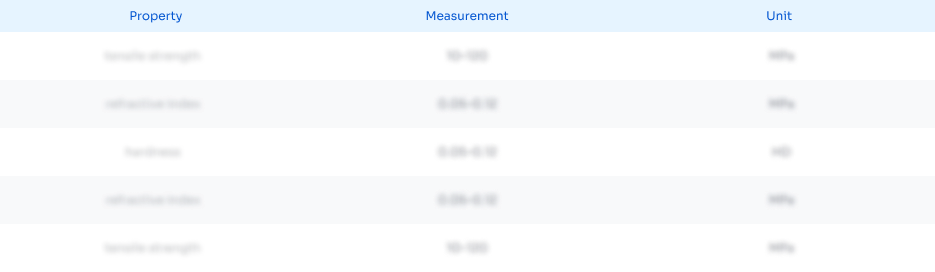
Abstract
Description
Claims
Application Information

- R&D
- Intellectual Property
- Life Sciences
- Materials
- Tech Scout
- Unparalleled Data Quality
- Higher Quality Content
- 60% Fewer Hallucinations
Browse by: Latest US Patents, China's latest patents, Technical Efficacy Thesaurus, Application Domain, Technology Topic, Popular Technical Reports.
© 2025 PatSnap. All rights reserved.Legal|Privacy policy|Modern Slavery Act Transparency Statement|Sitemap|About US| Contact US: help@patsnap.com