Modal test and parameter identification method for single-shaft ball screw feeding mechanical system
A technology of ball screw and mechanical system, which is applied in the field of feed drive experiment testing, can solve the problems that can only be obtained, but it is difficult to completely eliminate the vibration signal pickup of CNC system and servo system, and rotary moving parts, so as to eliminate the influence of electrical links , high precision and wide versatility
- Summary
- Abstract
- Description
- Claims
- Application Information
AI Technical Summary
Problems solved by technology
Method used
Image
Examples
Embodiment Construction
[0027] The present invention will be further described below with reference to the accompanying drawings.
[0028] refer to figure 1 , the auxiliary clamping device that the present invention adopts comprises auxiliary clamping device upper piece 3 and auxiliary clamping device lower piece 4, and auxiliary clamping device upper piece 3 and auxiliary clamping device lower piece 4 are connected by fastening bolt 2, nut 5 , the auxiliary clamping device is used to provide auxiliary functions for exciting and picking up vibrations of rotating parts (such as motor rotors, lead screws, etc.); when in use, loosen the nut 5 on one side of the device, and put the auxiliary clamping device on at the test position of the rotor or lead screw, e.g. figure 2 As shown, the auxiliary clamping device is located at the installation position of the ball screw feeding mechanical system. Installation position 9, installation position 10 of the auxiliary clamping device at the right end of the l...
PUM
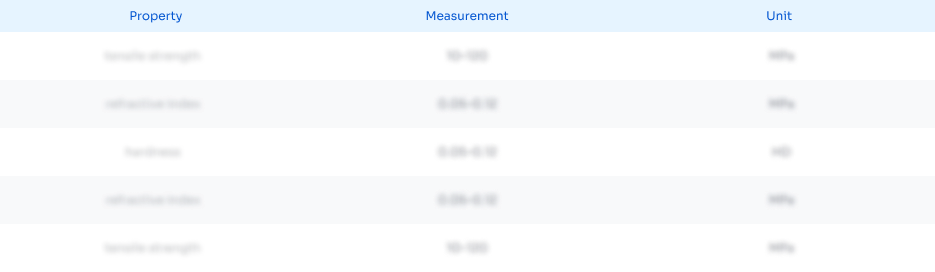
Abstract
Description
Claims
Application Information

- R&D Engineer
- R&D Manager
- IP Professional
- Industry Leading Data Capabilities
- Powerful AI technology
- Patent DNA Extraction
Browse by: Latest US Patents, China's latest patents, Technical Efficacy Thesaurus, Application Domain, Technology Topic, Popular Technical Reports.
© 2024 PatSnap. All rights reserved.Legal|Privacy policy|Modern Slavery Act Transparency Statement|Sitemap|About US| Contact US: help@patsnap.com