A grid-connected current control method applied to lcl type rectification feedback unit
A current control and feedback unit technology, applied in the direction of converting AC power input to DC power output, electrical components, output power conversion devices, etc., can solve the gain limitation of grid-connected current control loop, increase the difficulty of system stability control, Increase the additional loss of the system and other problems to achieve the effect of alleviating the impact, improving the stability margin, and increasing the gain
- Summary
- Abstract
- Description
- Claims
- Application Information
AI Technical Summary
Problems solved by technology
Method used
Image
Examples
Embodiment Construction
[0051] The present invention will be described in detail below in conjunction with the accompanying drawings and specific embodiments.
[0052] The present invention is a grid-connected current control method applied to an LCL rectifier feedback unit. The AC side current control system includes a main circuit part and a control circuit part. The topology of the main circuit is as follows: figure 1 As shown, the actual power grid system is inductive, and L in the figure g is the grid-side equivalent inductance, then the actual sampling point of the grid voltage is the common coupling point PCC, and the common coupling point voltage v pcc After the LCL filter, and then the rectifier output DC voltage V dc , the DC voltage is filtered by a capacitor to obtain the final output voltage, as can be seen from Figure 1, L 1 is the grid-connected side inductance, and the control object of the present invention is L 1 The current on the grid, that is, the grid-connected current i L1 ...
PUM
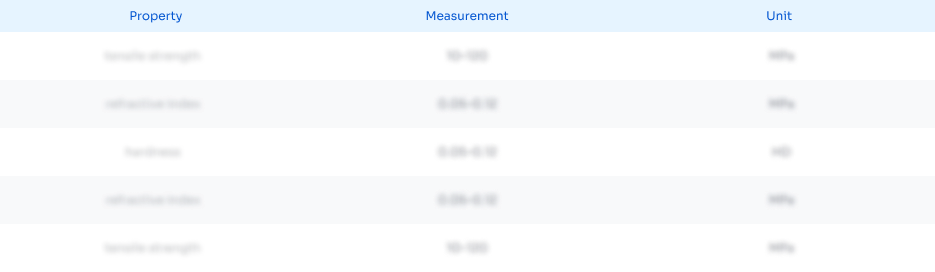
Abstract
Description
Claims
Application Information

- Generate Ideas
- Intellectual Property
- Life Sciences
- Materials
- Tech Scout
- Unparalleled Data Quality
- Higher Quality Content
- 60% Fewer Hallucinations
Browse by: Latest US Patents, China's latest patents, Technical Efficacy Thesaurus, Application Domain, Technology Topic, Popular Technical Reports.
© 2025 PatSnap. All rights reserved.Legal|Privacy policy|Modern Slavery Act Transparency Statement|Sitemap|About US| Contact US: help@patsnap.com