A kind of lye multistage recovery process
A lye and process technology, applied in the fields of papermaking and viscose fiber production, can solve the problems of decreased filtration efficiency, increased viscosity of waste lye, large pressure difference between the inlet and outlet of nanofiltration membranes, etc. Inlet viscosity, the effect of reducing the differential pressure of the membrane layer
- Summary
- Abstract
- Description
- Claims
- Application Information
AI Technical Summary
Problems solved by technology
Method used
Image
Examples
Embodiment 1
[0043]A multi-stage recovery process for lye includes the following steps:
[0044]Primary dilution: Dilute the viscose waste liquid to a primary dilution with a sodium hydroxide concentration of 85g / L and a hemicellulose concentration of 30g / L;
[0045]First-level filtration: pass the first-level diluent into the nanofiltration system I, set the temperature in the nanofiltration system I to 47℃, pressure to 17MPa, and control the membrane pressure difference to 2.5bar. After nanofiltration, a first-level concentrated solution is obtained. And first-level filtrate;
[0046]The concentration of sodium hydroxide in the primary concentrate is 85g / L, the concentration of hemicellulose is 60g / L, and the concentration of sodium hydroxide in the primary filtrate is 85g / L;
[0047]Secondary dilution: Dilute the primary concentrate to a secondary dilution with a sodium hydroxide concentration of 40g / L and a hemicellulose concentration of 30g / L;
[0048]Primary heating: heating the secondary diluent to 49℃;...
Embodiment 2
[0058]A multi-stage recovery process for lye includes the following steps:
[0059]Primary dilution: Dilute the viscose waste liquid to a primary dilution with a sodium hydroxide concentration of 90g / L and a hemicellulose concentration of 35g / L;
[0060]First-level filtration: pass the first-level diluent into the nanofiltration system I, set the temperature in the nanofiltration system I to 49℃, pressure to 18MPa, and control the membrane pressure difference to 2.2bar. After nanofiltration, the first-level concentrated liquid and Primary filtrate
[0061]The concentration of sodium hydroxide in the primary concentrate is 90g / L, the concentration of hemicellulose is 70g / L, and the concentration of sodium hydroxide in the primary filtrate is 90g / L;
[0062]Secondary dilution: Dilute the primary concentrate to a secondary dilution with a sodium hydroxide concentration of 45g / L and a hemicellulose concentration of 35g / L;
[0063]Primary heating: heating the secondary diluent to 51℃;
[0064]Secondary fi...
Embodiment 3
[0073]A multi-stage recovery process for lye includes the following steps:
[0074]Primary dilution: dilute the viscose waste liquid into a primary dilution with a sodium hydroxide concentration of 86g / L and a hemicellulose concentration of 31g / L;
[0075]First-level filtration: pass the first-level diluent into the nanofiltration system I, set the temperature in the nanofiltration system I to 48℃, pressure to 17MPa, and control the membrane pressure difference of 2.3bar. After nanofiltration, the first-level concentrated liquid and Primary filtrate
[0076]The concentration of sodium hydroxide in the primary concentrate is 86g / L, the concentration of hemicellulose is 62g / L, and the concentration of sodium hydroxide in the primary filtrate is 86g / L;
[0077]Secondary dilution: Dilute the primary concentrate to a secondary dilution with a sodium hydroxide concentration of 42g / L and a hemicellulose concentration of 31g / L;
[0078]Primary heating: heating the secondary diluent to 49℃;
[0079]Secondary ...
PUM
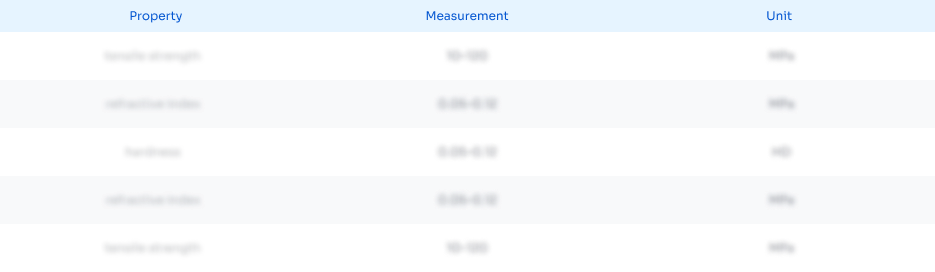
Abstract
Description
Claims
Application Information

- R&D
- Intellectual Property
- Life Sciences
- Materials
- Tech Scout
- Unparalleled Data Quality
- Higher Quality Content
- 60% Fewer Hallucinations
Browse by: Latest US Patents, China's latest patents, Technical Efficacy Thesaurus, Application Domain, Technology Topic, Popular Technical Reports.
© 2025 PatSnap. All rights reserved.Legal|Privacy policy|Modern Slavery Act Transparency Statement|Sitemap|About US| Contact US: help@patsnap.com