Method and tooling for processing hydraulic cylinder with joint seat
A processing method and technology of hydraulic cylinders, applied in metal processing equipment, metal processing machinery parts, manufacturing tools, etc., can solve the problems of inability to ensure personnel safety, affecting cylinder processing efficiency, affecting production efficiency, etc., so as to reduce machining waste. The effect of reducing material cost and improving production efficiency
- Summary
- Abstract
- Description
- Claims
- Application Information
AI Technical Summary
Problems solved by technology
Method used
Image
Examples
Embodiment Construction
[0038] The technical solutions of the present invention will be described in further detail below through specific implementation methods.
[0039] Such as Figure 1-Figure 5 As shown, a method for processing a hydraulic cylinder with an upper cavity joint seat is carried out according to the following steps:
[0040] 1) Cylinder blanking, use a sawing machine or a circular saw to cut and blank, and reserve a machining allowance of 4-6mm for the total length.
[0041] 2) Tailor-welding the joint seat 8 of the upper cavity, this step is carried out in two steps;
[0042] 2.1) Tooling adjustment before welding, the tooling includes L-shaped positioning plate 2, positioning pin 3 and lock nut 4, and the horizontal plane 5 of the L-shaped positioning plate is set and adjusted correspondingly to the locking nut 4 and positioning pin 3 The long slot 7, the positioning pin 3 can slide in the adjustment long slot 7 to adjust the specific position of the positioning pin 3; the vertic...
PUM
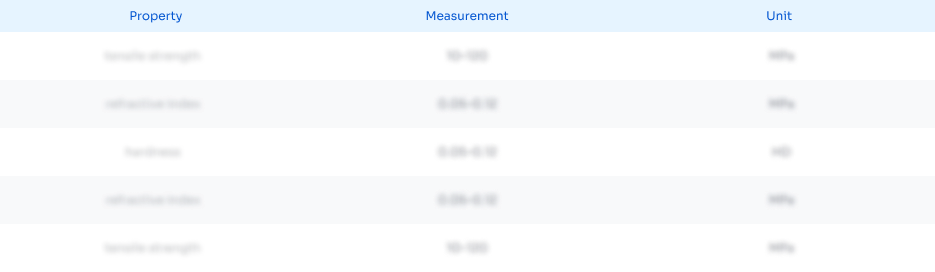
Abstract
Description
Claims
Application Information

- R&D Engineer
- R&D Manager
- IP Professional
- Industry Leading Data Capabilities
- Powerful AI technology
- Patent DNA Extraction
Browse by: Latest US Patents, China's latest patents, Technical Efficacy Thesaurus, Application Domain, Technology Topic, Popular Technical Reports.
© 2024 PatSnap. All rights reserved.Legal|Privacy policy|Modern Slavery Act Transparency Statement|Sitemap|About US| Contact US: help@patsnap.com