Bearing pre-tightening device
A technology of pressing device and bearing, applied in the direction of bearing element, shaft and bearing, rigid bracket of bearing component, etc., can solve the problems of complex structure and large installation workload, etc.
- Summary
- Abstract
- Description
- Claims
- Application Information
AI Technical Summary
Problems solved by technology
Method used
Image
Examples
Embodiment 1
[0032] figure 1 It is a structural schematic diagram of the bearing pretensioning device of the present invention. figure 2 It is a structural schematic diagram of the elastic element in Embodiment 1 of the bearing pretensioning device of the present invention.
[0033] Such as figure 1 and figure 2 As shown, the present invention discloses a bearing pretensioning device 10 , which includes a bearing seat 11 , two bearings 12 and a shaft sleeve 13 . Wherein, the bearing 12 is installed in the bearing seat 11, and is installed on the shaft 14 through the shaft sleeve 13, so that the bearing 12 is axially positioned. At the same time, a compression device 15 is provided on the bearing seat 11, and the outer ring of the bearing 12 is compressed by the compression device 15. An elastic element 16 is arranged between the two bearings 12, and the elastic element 16 is deformed under pressure to compress the outer ring of the bearing 12. The outer ring of the bearing 12 applies...
specific Embodiment
[0037] For example, the specific dimensions of the elastic element 16 can be set as an outer diameter of 158mm, a width of 28mm, a material elastic modulus E of 2E11Pa, and a Poisson's ratio of 0.3.
[0038] One of the advantages of this structure is that the stiffness can be adjusted by adjusting the cross-sectional area of the spring wire, the bending structure of the spring wire, and the number n of the spring wire without changing the main dimensions of the structure.
[0039] Through the finite element method and Hooke's theorem, the stiffness of the elastic element can be calculated, and the calculation result is:
[0040] The number of spring wires is n=3, when the section of the spring wire is 2mm×8mm, the stiffness is 2.6E6N / m;
[0041] The number of spring wires is n=54, when the spring wire section is 2mm×8mm, the stiffness is 4.67E7N / m;
[0042] The number of spring wires is n=54, when the section of the spring wire is 4mm×8mm, the stiffness is 6.69E8N / m;
[00...
Embodiment 2
[0046] image 3 It is a structural schematic diagram of the elastic element in Embodiment 2 of the bearing pretensioning device of the present invention.
[0047] Such as image 3 As shown, the structure of this embodiment is basically the same as that of Embodiment 1, the difference is that: the elastic wire 162 of the elastic element 16 in the bearing pretensioning device of this embodiment is in a "W" shape. Or, on this basis, the elastic wire 162 can also be arranged in a continuous wave shape.
[0048] The elastic element of this one-piece cage structure occupies less space, is easy to install, and has a wide range of stiffness, which can generate a wide range of axial force and realize the application of bearing preload. It is suitable for multiple bearings with different deformation and preload. kind of occasion.
PUM
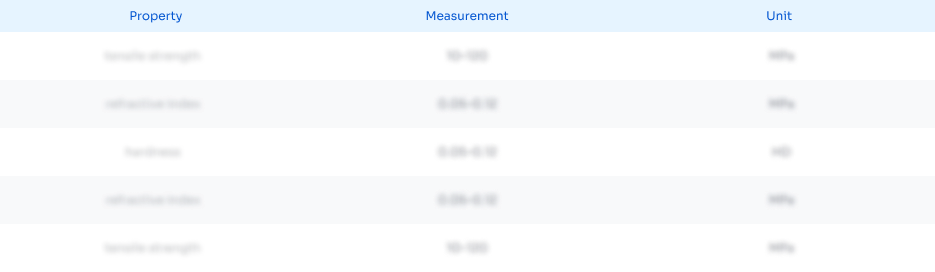
Abstract
Description
Claims
Application Information

- R&D
- Intellectual Property
- Life Sciences
- Materials
- Tech Scout
- Unparalleled Data Quality
- Higher Quality Content
- 60% Fewer Hallucinations
Browse by: Latest US Patents, China's latest patents, Technical Efficacy Thesaurus, Application Domain, Technology Topic, Popular Technical Reports.
© 2025 PatSnap. All rights reserved.Legal|Privacy policy|Modern Slavery Act Transparency Statement|Sitemap|About US| Contact US: help@patsnap.com