Preparation method of base material for foam tape
A base material and tape technology, which is applied in the field of foam tape base material preparation, can solve the problems affecting the use quality, appearance and aesthetics of the foam tape, and achieve the advantages of increased aesthetics, low production cost and strong practicability Effect
- Summary
- Abstract
- Description
- Claims
- Application Information
AI Technical Summary
Problems solved by technology
Method used
Image
Examples
Embodiment 2
[0029] The operation steps of this embodiment are as follows:
[0030] 1. Put the raw materials of the foam tape substrate including 45 parts of linear low density polyethylene, 35 parts of polyurethane, 15 parts of hydrolysis-resistant components, 3 parts of coupling agent, 15 parts of foaming agent and 3 parts of antistatic agent into mixing Mix in the machine, and granulate at a certain temperature to make the base material masterbatch;
[0031] 2. Add the antistatic agent and use water to prepare a solution with a mass fraction of 2%;
[0032] 3. Add the solution in step 2 to the spray equipment, spray the environment of the extrusion molding process, and then send the base material masterbatch in step 1 into the extrusion molding equipment, and extrude at a uniform speed to form a sheet ;
[0033] 4. Soak the sheet in step 3 in the solution in step 2. The upper surface of the solution is 1mm above the upper surface of the sheet, soak for 3 hours, then take it out and us...
Embodiment 3
[0037] The operation steps of this embodiment are as follows:
[0038] 1. Put 30 parts of linear low-density polyethylene, 30 parts of polyurethane, 30 parts of hydrolysis-resistant components, 1 part of coupling agent, 15 parts of foaming agent, and 1 part of antistatic agent into the kneading process Mix in the machine, and granulate at a certain temperature to make the base material masterbatch;
[0039] 2. Add the antistatic agent and use water to prepare a solution with a mass fraction of 2%;
[0040] 3. Add the solution in step 2 to the spray equipment, spray the environment of the extrusion molding process, and then send the base material masterbatch in step 1 into the extrusion molding equipment, and extrude at a uniform speed to form a sheet ;
[0041] 4. Soak the sheet in step 3 in the solution in step 2. The upper surface of the solution is 1mm above the upper surface of the sheet, soak for 2 hours, then take it out and use air-drying treatment, the wind speed is ...
PUM
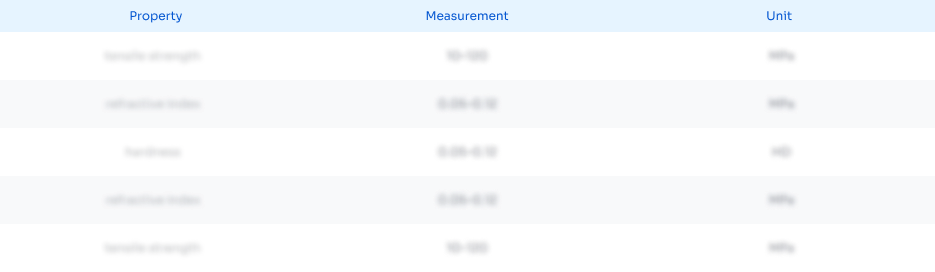
Abstract
Description
Claims
Application Information

- Generate Ideas
- Intellectual Property
- Life Sciences
- Materials
- Tech Scout
- Unparalleled Data Quality
- Higher Quality Content
- 60% Fewer Hallucinations
Browse by: Latest US Patents, China's latest patents, Technical Efficacy Thesaurus, Application Domain, Technology Topic, Popular Technical Reports.
© 2025 PatSnap. All rights reserved.Legal|Privacy policy|Modern Slavery Act Transparency Statement|Sitemap|About US| Contact US: help@patsnap.com