Non-isothermal forming device and technique for continuous fiber reinforced thermoplastic composite material
A technology for reinforcing thermoplastic and continuous fibers, applied in the field of hot stamping of continuous fiber reinforced thermoplastic resin matrix composites, can solve the problems of prolonging heating and cooling time, affecting mold life, reducing work efficiency, etc., to improve flexibility, improve The effect of forming processing efficiency and reducing equipment cost
- Summary
- Abstract
- Description
- Claims
- Application Information
AI Technical Summary
Problems solved by technology
Method used
Image
Examples
Embodiment 1
[0040] Taking three-layer unidirectional carbon fiber fabric reinforced nylon hot stamping as an example (see figure 1 ).
[0041] Correctly install the mold and all parts of the components (see image 3), cut the unidirectional prepreg into a square with a side length of 120mm, clean the surface of the prepreg with a brush, and then dry it in a 40°C oven for 5 minutes, and stack it according to the method of [0° / 90° / 0°] layer. Apply an appropriate amount of methyl silicone oil evenly on the surface of the blank holder and the die that is in contact with the blank, then put the blank into the groove of the die, and install it with the blank holder at the same time. From top to bottom, the blank holder, The sequence of the blank and the die should be placed in coordination (see Figure 4 ). Preheat the combination of blank holder, blank and die together in an oven at 280°C, make it pre-pressed under a load of 20Kg for 5 minutes, and then keep it in a furnace at 240°C for 10...
PUM
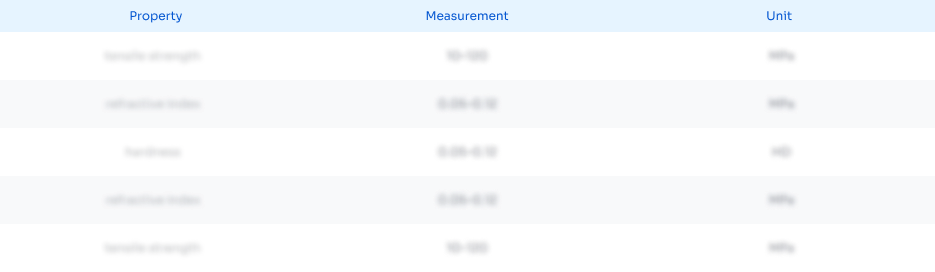
Abstract
Description
Claims
Application Information

- R&D Engineer
- R&D Manager
- IP Professional
- Industry Leading Data Capabilities
- Powerful AI technology
- Patent DNA Extraction
Browse by: Latest US Patents, China's latest patents, Technical Efficacy Thesaurus, Application Domain, Technology Topic, Popular Technical Reports.
© 2024 PatSnap. All rights reserved.Legal|Privacy policy|Modern Slavery Act Transparency Statement|Sitemap|About US| Contact US: help@patsnap.com